Standard end-of-line test systems are effective at detecting obvious issues such as bearing faults. However, subtle and rare acoustic anomalies – caused by factors like assembly misalignments, gear tooth damage, or breakage – often go undetected. Electric motors, in particular, are vulnerable to performance deviations resulting from variations in magnetic field strength, increased cogging torque, torque ripple, and inverter-induced noise.
Moreover, noise quality issues such as gear rattle or whining may not directly jeopardize the functionality of the unit under test, but they can significantly impact user experience and brand perception. Consistently monitoring these acoustic characteristics across a wide range of test units is essential. The evolving acoustic profile of each unit offers valuable insights into the long-term trends and stability of production quality.
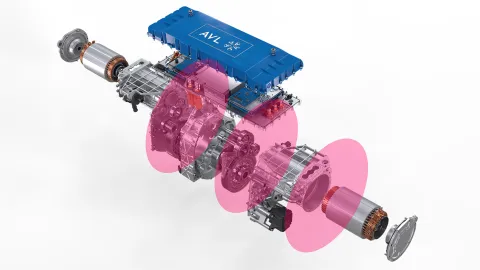
Detect Subtle and Rare Acoustic Anomalies
Go beyond standard fault detection to identify infrequent or nuanced issues.
Assess Noise Quality Impact
Capture and evaluate non-critical noises (e.g. gear rattle) that affect user experience and brand perception.
Enable Long-Term Acoustic Monitoring
Track acoustic profiles across multiple tests to assess production quality trends and emerging patterns.
With AVL AQC, NVH testing at the end of the production line goes beyond standard checks – capturing a wider spectrum of noise, vibration, and harshness issues. By identifying and documenting even the rarest acoustic anomalies, manufacturers gain deeper insights into component quality. The more NVH data collected, the more accurate the predictions and the earlier potential issues can be addressed. In the long run, precise and consistent NVH measurements are one of the most effective strategies for reducing costly vehicle recalls and safeguarding brand reputation
The system includes the following key components
- Test System Automation (PUMA 2 or 3rd party)
- Sensor Positioning System (e.g., robot arm)
- Sensors (e.g. microphone, laser vibrometer or
conventional vibration sensors) - Data acquisition AVL X-Meter and AVL IndiCom™
- Postprocessing Software AVL CONCERTO
Application | Designed to deal with high production volume |
E-Axle handling | Manual or (semi-) automatic |
Takt time | Typically 2-5 min. |
Automation | AVL PUMA 2™ Production |
Data acquisition | AVL IndiCom™ |
Post-processing | AVL CONCERTO™ including NVH Toolbox and Statistical Tool |
Measurement variables | Air-borne and structrue-borne noise phenomena besides typical UUT load information (dynamic torque, speed, ...) |
Sensors | Accelerometers, microphones, laser-vibrometers or customer specific equipment |
Environment integration | Seamslessly integrable into the customer production line |
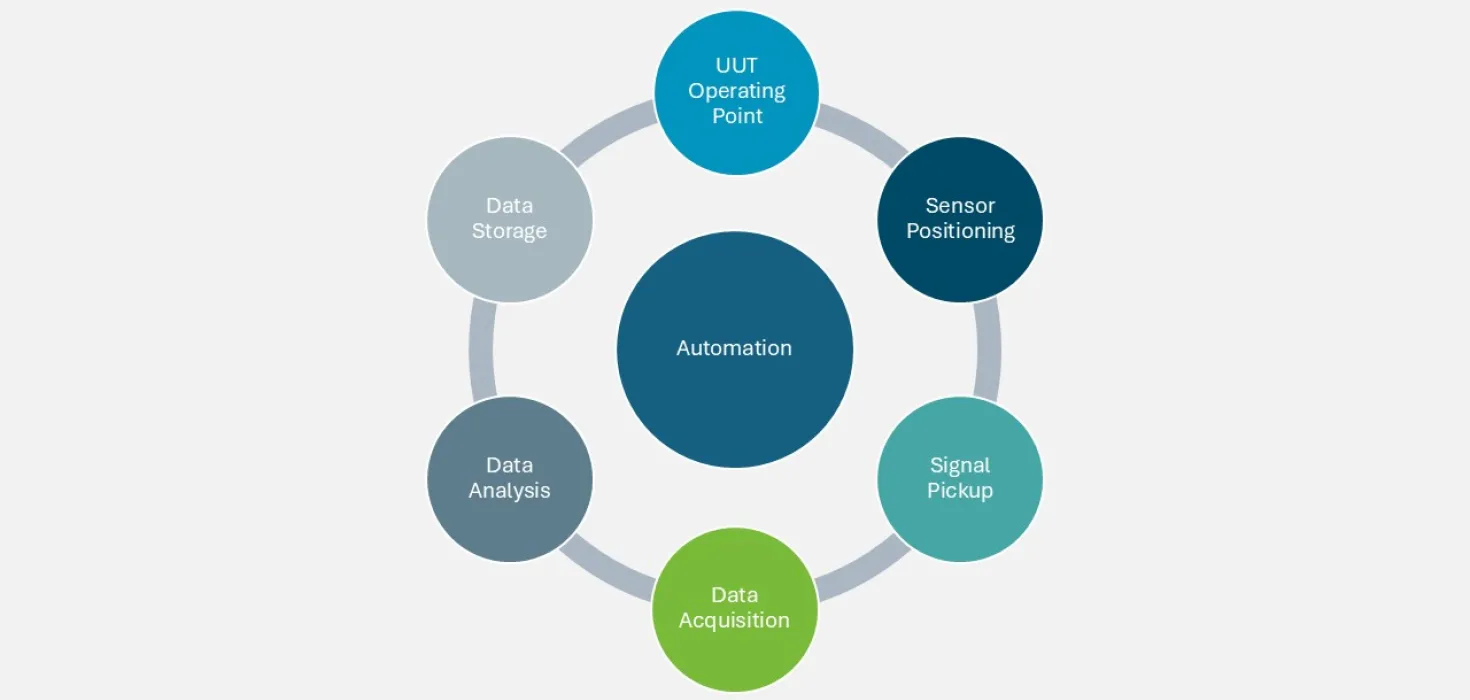
The AVL AQC combines intelligent automation with precision measurement to streamline end-of-line NVH testing. The process begins with PUMA™, which sets the test object into a defined operating state – such as specific speed, torque, power, or temperature. Next, the positioning system places or aligns the sensor precisely, depending on its type and the test requirements. The captured signal is then processed by IndiCom™ and validated by PUMA™. At the end of the cycle, a comprehensive report confirms whether the unit under test meets the quality acceptance criteria, clearly indicating whether it is OK or NOK. This seamless workflow ensures consistent, reliable, and fully automated acoustic quality control.
Pinpoint Precision with Advanced NVH Analysis
Catch the Unexpected – Detect spontaneous noise events like clicks or ticks with our unique impulsive noise feature.
Reveal the Hidden – Identify rare and subtle acoustic anomalies that traditional systems often miss – ensuring no defect slips through.
Seamless Integration from Sensor to Insight
All-in-One Solution – From signal acquisition to data evaluation, AVL AQC delivers a fully integrated hardware and software ecosystem. No More Sync Issues – A unified platform means smooth operation, easy updates, and a future-proof investment in quality control.
Flexible, Scalable, and Built for Your Needs
Tailored Testing – Easily adapt sensors and evaluation methods to your specific production requirements. Expandable Architecture – Scale effortlessly as your testing needs grow. Smart Data Management – Intelligent threshold and data handling for efficient, adaptive quality monitoring.
Data-Driven Traceability That Lasts
Consistent Comparisons – Benchmark results across test units and production stages using standardized procedures.
Fast, Insightful Evaluation – A dynamic database enables rapid access to historical data and trends – empowering continuous improvement.
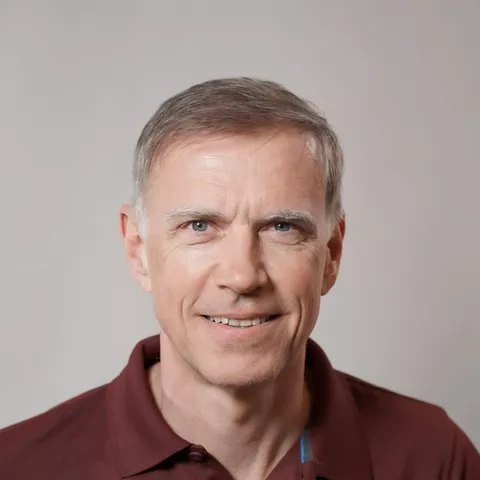
During end-of-line (EOL) testing, we utilize advanced NVH analysis to identify production errors that significantly impact customer acceptance. Our AVL system for acoustic quality control provides the essential toolchain for detecting both standard and unforeseen NVH issues in EOL testing.”
– Gerhard Zalar, Senior Application Engineer, AVL List GmbH
AVL Production Testing Solutions – Brochure
Quality in Time.