The shift to electrification presents a number of challenges for the test system: Rapid market demands are shortening development cycles to stay ahead of the competition. Another challenge is space, as existing facilities optimized for internal combustion engines have a limited footprint and must be repurposed for electrified axles. New CO2 legislation is increasing the development effort for all powertrains based on internal combustion engine technology. Finally, electrified powertrains present new challenges at higher frequencies that are not fully reproduced on the testbed. Using the same tool chain throughout the development process makes it easy to integrate the testbed.
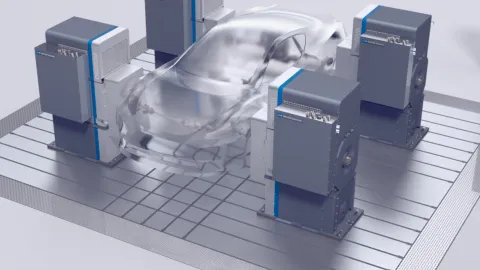
Our answer to these challenges is AVL SPECTRA with its quantum leap technology based on SiC and Field Programmable Gate Array (FPGA) technologies. This leads to high switching frequencies of up to 48 kHz coupled with control frequencies up to 192 kHz.
High control dynamics enables simulation models to be calculated with the highest possible speed – enhancing simulation capabilities such as inertia simulation. The control dynamics is coupled with the matching dyno performance of asynchronous machines making it suitable for all typical electrified powertrains from 3,200 Nm up to over 5,000 Nm nominal torque.
SiC technology allows the AVL SPECTRA converter to be integrated in the smallest possible installation space as the footprint has been reduced compared to conventional converters.
The SPECTRA application framework allows a consistent toolchain to be used throughout your development process – use your MATLAB Simulink models for the optimization of NVH, EMC, etc., and run them directly on the SPECTRA control unit.
Active Front End |
Nominal Values |
SPECTRA AFE 440 |
440 kVA |
SPECTRA AFE 880 |
880 kVA |
Dynamometers |
Nominal Values |
ASM 3250 | 3,250 Nm, 220 kW |
ASM 5000 | 5,000 Nm, 440 kW |
Highest Development Efficiency
By using SiC and FPGA, high control and switching frequencies can be achieved. This allows the testbed to follow demand values with the highest possible precision.
Outstanding Test Certainty
Bringing control dynamics to a new level enables testing to be as close as possible to real road conditions.
Maximum Flexibility on the Testbed
Large application variety with inertia simulation ensures maximum flexibility on the testbed using higher inertia asynchronous machines (ASM) with SPECTRA technology.
Space and Cost Saving
50% smaller converter cabinet space facilitates a wide range of upgrade scenarios for existing test cells, supporting your path to electrification.
Superior Control
The ultra-fast 1MHz control cycle reduces dead times and allows execution of highly dynamic test cases. In addition, it enables inertia simulation which widens the field of application for your testbed.
High Switching Frequency Without Derating
The fully water-cooled SiC power electronics are capable of high switching frequencies without the drawback of current derating.
AVL SIGNATURE Line – Brochure
Superior Technology – with AVL SPECTRA™ Inside.
AVL E-Mobility Testing Solutions – Brochure
From battery to full vehicle, from products, to test systems to whole test facilites – learn how we can support your testing needs.
AVL SPECTRA™ E-Motor Dyno – Solution Sheet
AVL SPECTRA™ E-Motor Dyno Converter – Solution Sheet
AVL SPECTRA™ Universal Inverter – Solution Sheet
Versatile testing device for future-proof e-motor and inverter development.
We are constantly working on new solutions. The following might be interesting for you:
Everything that excels at a glance: AVL highlights you shouldn't miss.