Battery reliability
Reliable prediction of battery behavior is extremely complex. Especially so when it covers the entire product lifecycle. This can only succeed with precise modeling of all effects that occur, such as breathing and swelling of cells, or age-related rise in resistance, and with corresponding parameter adjustments.
Battery safety
The swift pace of innovation in battery technologies also increases safety-related demands – an aspect that is often decisive for end users. Manufacturers need to use innovative testing and simulation methods to keep up with these rapidly changing requirements.
Value, profitability, and operating costs
In light of increasing cost pressure, most manufacturers are facing the challenge of reducing overall operating costs while also achieving improved battery value and profitability. This is made possible by intelligent data entry and fleet monitoring.
Efficiency in development
Short commercial rollout times paired with high safety standards – these objectives are often difficult to combine in practice. To guarantee both, simulation is the ideal way to swiftly validate the battery design at an early stage.
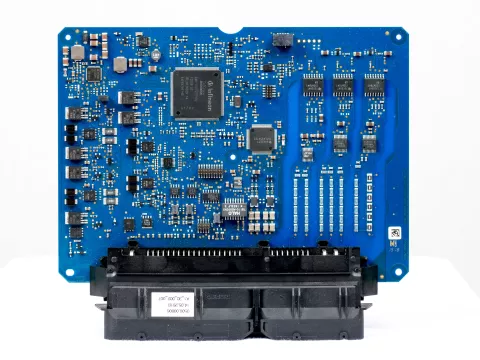
Our BMS is built on the experience accumulated at AVL over more than 15 years of battery development. The system is being developed continuously, and the fourth generation is now available. The next upgrade will provide additional core functions with even more precise predictive models.
State of Charge (SOC):
- Increased accuracy for lithium ferro-phosphate (LFP) batteries
- Non-linear dynamic modeling
- Optimal experiment design to reduce testing and calibration effort
State of Health (SOH):
- Implementation of a model to predict aging and durability
- Combination of SOH monitoring and durability prediction to increase precision and robustness
State of Function (SOF):
- Continuous calculation of current functional state
- Optimization of operational strategy to reach target durability, for example
- Adjustment of SOF based on predicted durability and SOH estimations
Hardware (control unit and module controller):
- Battery control unit with integrated high-voltage measurement and contactor control
- Module controllers for up to 18 cells in series with a board footprint of 70 x 90 mm
- Complete hardware and software implementation for ISO26262
- For batteries up to 1000V and subpacks with parallel processing
Implementation
The BMS of AVL has already proved itself in numerous customer projects. It is available as a self-contained black box solution, and in an open white box version, for seamless integration into your development and tool environment.
Virtual validation
Our validation is as broad as possible to fulfill all legal standards and specifications. It ranges from thermal-electric and mechanical design simulations to electromagnetic compatibility (EMC) and NVH simulations (noise, vibration, harshness) and the complete virtual validation environment.
Predictive BMS
You can use our BMS to make precise predictions about the energy requirements of your battery system. Thresholds can be adjusted flexibly at any time, based on changing infrastructure data.
Communication and interfaces
The battery management system is connected to the battery master control unit (BMCU), either directly using a wired powerline, e.g. SPI, or completely wirelessly. Reducing connections avoids sources of errors and saves costs.
Modular system offering
By choosing our BMS, you are opting for a modular system. This helps you to add value and profitability to the battery, optimize the charging strategy, and increase workshop efficiency. You also enable cost-efficient battery replacement and reduce the total cost of ownership.
Virtual battery development tools
Our many years of expertise with simulations and the associated tools guarantee an efficient development process. You benefit from clear frontloading of tasks, with rapid validation at an early stage.
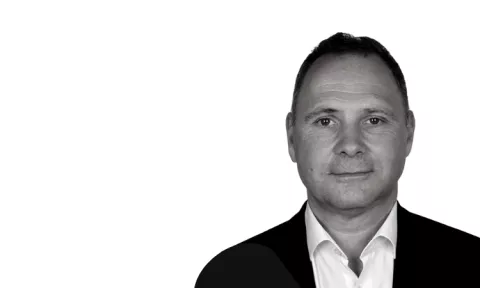
Embedding cells is pivotal in preventing battery aging. And a high-performance battery management system is key. This enables the dynamic load limits to be shifted, depending on the operational aging risk. Our tools are able to simulate most of these factors, allowing us to predict them virtually and take them into account in the development process.
– Jürgen Schneider, Senior Solution Manager Virtual Battery Development
Related Topics
We are constantly working on new solutions. The following might be interesting for you: