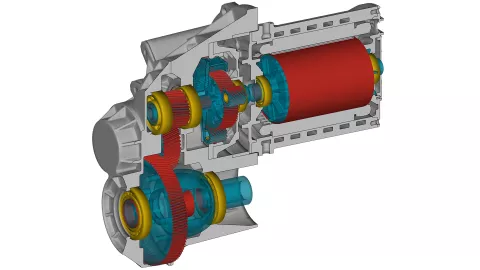
Through the highest fidelity simulation approach our solution enables the accurate prediction of e-drive NVH. It covers the complete workflow from design to acoustics. The simulation runs in time domain which enables the consideration of physical behavior like it is in reality, without the need to simplify (linearize).
Electromagnetic excitations are indispensable in NVH simulations, but these forces are often difficult to obtain or even not available at all because many electromagnetic simulation tools don’t provide them as a standard output. Our solution comes with a tool which gives multi-body simulation engineers the possibility to calculate electromagnetic forces without expertise in the field.
The e-drive creates tonal noise (a constant frequency at certain speed), which can be annoying to the passengers of the car. In BEVs these sounds are not masked by broadband noise, since there is no ICE. This makes the unwanted noise phenomena even more prominent.
The first step in addressing this issue is to conduct a thorough root cause analysis. It is important to understand the source of the NVH excitation and how it is transmitted through the e-drive structure and on to the passenger's ears. This knowledge enables engineers to change the design to minimize the excitations.

Accurately predict NVH
You can be sure that all physical effects have been considered, giving the engineer confidence in the simulation results.
Optimize the E-drive
Virtual design and optimization leads to a reduction in testing, saving time and money.
Consider Production Tolerances
Simulation can create perfect conditions that do not exist in reality. Our solution virtually identifies critical drive factors and incorporates real-world manufacturing tolerances - such as bearing race offset or planetary gear assembly misalignment.
Obtain Electromagnetic Excitations
Electromagnetic excitations that are sometimes difficult to obtain are provided by the AVL E-Motor Tool.
Consider Important NVH Factors
Key contributors to e-drive NVH behavior like gear and roller bearing contacts and e-motor excitations are considered in high detail.
Easily import your initial transmission design from FVA-Workbench and other design tools into our solution with just two clicks using the REXS data format and generate any missing electromagnetic excitation.
To ensure model accuracy and establish initial parameters, an initial kineto-static simulation is conducted.
This is followed by a dynamic simulation in the time or frequency domain. Results, presented as graphs or 3D animations, include all bodies and interactions such as gears and bearings.
In addition, the results of the housing surface vibration are fed into our acoustics solution, which calculates airborne noise and provides sound pressure level at microphone positions.
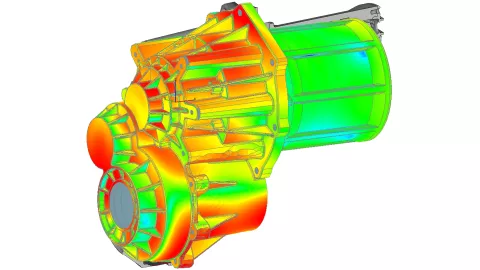
Profit from AVL’s decades of experience in powertrain development. Experience that we have built into our software.
Highest Fidelity Simulation
The model approach for e-axle with full body flexibility and physical contact modeling guarantees the highest level of accuracy. The results are e-drive NVH predictions you can rely on for decision-making.
Complete Workflow
The solution covers the workflow from initial design to acoustics, including the generation of electromagnetic excitation.
Easy Integration
It can be easily integrated into existing workflows (or automated via COMPOSE Apps). Import existing designs from various tools, using the REXS data format.
E-Drive Dynamics with Gear and Bearing Contacts
AVL EXCITE™ M runs multi-body dynamics in time domain. It solves gear and bearing contacts simultaneously with flexible body motion and deformation. Our solution solves high fidelity models in short time with its best-in-class solver.
Transient E-Drive Dynamics
Consider e-drive transient operating conditions in the dynamic simulation, including the influence of the controllers. Define relevant boundary conditions directly in EXCITE M or easily couple to vehicle simulation tools.
Streamlined NVH Workflow from excitation to air borne noise
Minimize structural vibrations and dynamic transmission errors to optimize NVH. EXCITE M offers a workflow that includes all steps from design and dynamic simulation to surface normal velocity. These values can be used to simulate air borne noise in AVL EXCITE Acoustics™.
Dynamic Electromagnetic Coupling
E-motor characteristic is pre-calculated with the electromagnetic simulation tool. The e-motor model is part of the electric circuit which includes simple controllers, and it is embedded in the EXCITE M model. Transient effects and influence of controller and rotor eccentricity can be considered.
Inverter Excitation (PWM influence)
Easy definition of inverter in e-motor joint of EXCITE M to investigate the effects of Pulse Width Modulation (PMW) on NVH. Avoid tonal excitations in terms of PWM strategies, overmodulation, use of constant or speed-dependent switching frequency, or a band for random switching frequency.