Nowadays, more and more vehicle programs are based on platform solutions. Saving weight, reducing parts, simplifying installation, service, and recycling aspects already play a major role here at module level. In this environment, our model-based developments offer ideal solutions to combine the highest possible level of energy density with low unit and production costs.
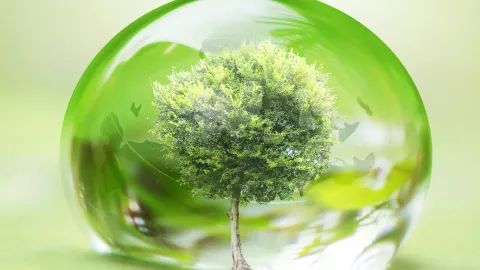
Fewer Components in the Battery System
The number of components can be effectively reduced with integrated cell-to-pack or cell-to-chassis solutions. The same applies for the electrification of the entire powertrain. The reduction in the amount of material used not only affects the cost structure, it also improves the bottom line for installation and reusability.
Improved Supply Chain Management
Normally, battery components with innovative functions and a low carbon footprint also require new production processes. They are also demanding with regard to scalability. This makes it even more challenging for many market players to build their own supply chains and circular supply and disposal processes.
New CO2 Guidelines
Batteries are destined to required by law to state their carbon footprint in the Life Cycle Assessment (LCA). This requires precise measurements in production and evaluations of suppliers and must also take into account raw materials based on recycled goods.
Swift Technology Cycles
Modern battery technology is characterized by rapid advances in development. Keeping pace with this requires the direct transfer of innovations to functional, series-ready products with industrial design.
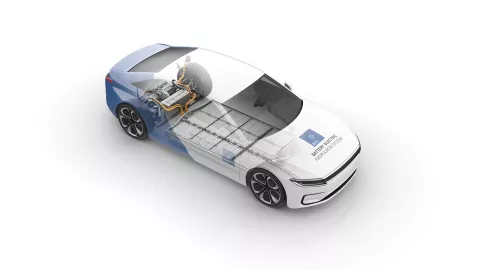
At AVL, we run a comprehensive, continuous benchmarking program for vehicle battery systems. This gives us a deeper understanding of current module and pack technologies, and enabled bay the flip of the well-known V process: Integration and verification go hand in hand with product design and component procurement, and the specification of requirements.
- Continuous benchmarking program for vehicle battery systems
- Reports, test data, workshops with immediate availability
- Four new vehicles per year: from low-budget to luxury xEVs
- All key reference characteristics contain: performance, security, efficiency, operational reliability, costs, producibility, ease of service, technical requirements
Standardized Concept Development
Our methodology for concept development has been market tested. It guarantees a quick start and efficient execution in terms of time. From the idea to a practical solution.
In-Depth Market Expertise
Thanks to our benchmarking program for vehicle innovations and close connections with many suppliers in and around customer projects, our internal research and development department is always focused on the battery market. This enables us to deliver a holistic information base for our customers.
Efficient Development of Battery Series
Early risk assessment and simulation-supported methods allow us to ensure development of preproduction, variants, and derivatives, streamlined in terms of costs and time – from the initial idea to the start of production.
New Battery Series Development
Make use of our development methodology for new battery series – from the first drawing to SOP. It is specifically tailored to current customer requirements and provides you with a proven combination of requirement management, risk assessment, simulation, and validation.
Development of Battery Derivatives
We offer solutions based on model-based system design, streamlined in terms of costs and time, specifically for the development of production and product variants. These deliver benefits for established manufacturers as well as for new market entrants.
Reach Your Objective in Eight Weeks
Our standardized process for the development of concepts for battery modules and packs provides you with advantages in projects under huge time pressure. It takes just eight weeks to get from the idea to the series-ready mainstream concept solution – including all of AVL’s expertise for the various battery applications.
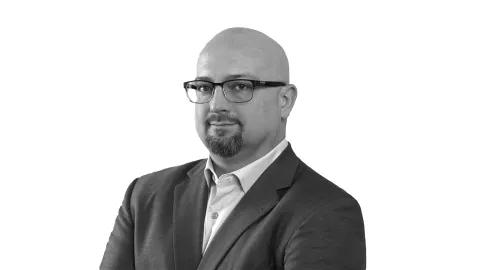
AVL upholds a strong focus on battery design and technology from the cell to large scale production ready energy systems. With the everchanging xEV market, we are continuously honing our strengths for tomorrow’s batteries and customer needs. Recent examples include exceeding thermal propagation regulation time by more than 14x, launching one of the first immersion cooled batteries into production, and utilizing data analytics for early warning anomaly detection.
– Adam Dendrinos, Senior Product Manager Battery Systems
Solution Sheet: Innovative Thermalmanagement
DownloadRelated Topics
We are constantly working on new solutions. The following might be interesting for you: