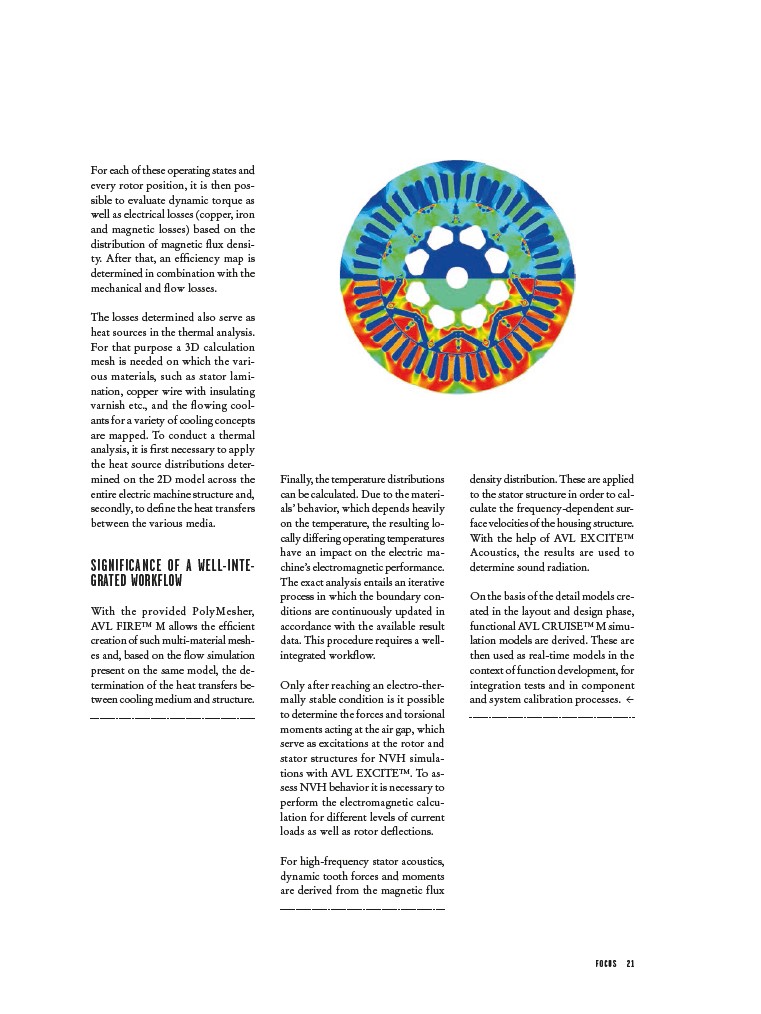
F O C U S 2 1
For each of these operating states and
every rotor position, it is then possible
to evaluate dynamic torque as
well as electrical losses (copper, iron
and magnetic losses) based on the
distribution of magnetic fl ux density.
After that, an effi ciency map is
determined in combination with the
mechanical and fl ow losses.
The losses determined also serve as
heat sources in the thermal analysis.
For that purpose a 3D calculation
mesh is needed on which the various
materials, such as stator lamination,
copper wire with insulating
varnish etc., and the fl owing coolants
for a variety of cooling concepts
are mapped. To conduct a thermal
analysis, it is fi rst necessary to apply
the heat source distributions determined
on the 2D model across the
entire electric machine structure and,
secondly, to defi ne the heat transfers
between the various media.
SIGNIFICANCE OF A WELL-INTEGRATED
WORKFLOW
With the provided PolyMesher,
AVL FIRE™ M allows the effi cient
creation of such multi-material meshes
and, based on the fl ow simulation
present on the same model, the determination
of the heat transfers between
cooling medium and structure.
Finally, the temperature distributions
can be calculated. Due to the materials’
behavior, which depends heavily
on the temperature, the resulting locally
differing operating temperatures
have an impact on the electric machine’s
electromagnetic performance.
The exact analysis entails an iterative
process in which the boundary conditions
are continuously updated in
accordance with the available result
data. This procedure requires a wellintegrated
workfl ow.
Only after reaching an electro-thermally
stable condition is it possible
to determine the forces and torsional
moments acting at the air gap, which
serve as excitations at the rotor and
stator structures for NVH simulations
with AVL EXCITE™. To assess
NVH behavior it is necessary to
perform the electromagnetic calculation
for different levels of current
loads as well as rotor defl ections.
For high-frequency stator acoustics,
dynamic tooth forces and moments
are derived from the magnetic flux
density distribution. These are applied
to the stator structure in order to calculate
the frequency-dependent surface
velocities of the housing structure.
With the help of AVL EXCITE™
Acoustics, the results are used to
determine sound radiation.
On the basis of the detail models created
in the layout and design phase,
functional AVL CRUISE™ M simulation
models are derived. These are
then used as real-time models in the
context of function development, for
integration tests and in component
and system calibration processes. <