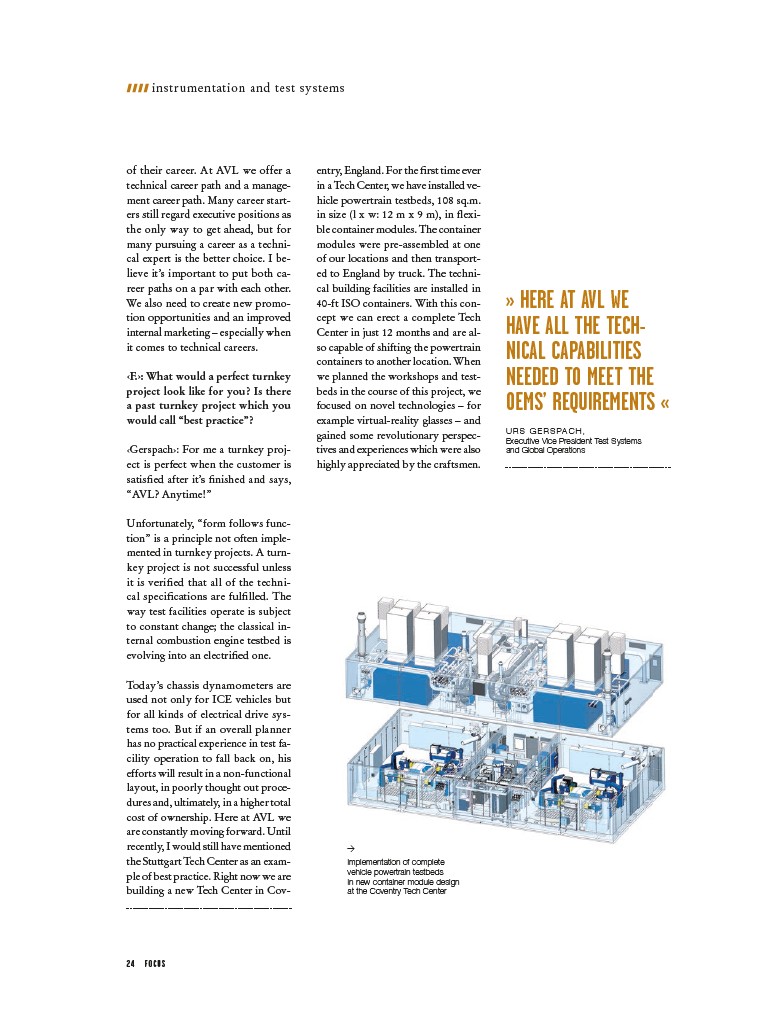
instrumentation and test systems
of their career. At AVL we offer a
technical career path and a management
career path. Many career starters
still regard executive positions as
the only way to get ahead, but for
many pursuing a career as a technical
expert is the better choice. I believe
it’s important to put both career
paths on a par with each other.
We also need to create new promotion
opportunities and an improved
internal marketing – especially when
it comes to technical careers.
‹F.›: What would a perfect turnkey
project look like for you? Is there
a past turnkey project which you
would call “best practice”?
‹Gerspach›: For me a turnkey project
is perfect when the customer is
satisfied after it’s finished and says,
“AVL? Anytime!”
Unfortunately, “form follows function”
is a principle not often implemented
in turnkey projects. A turnkey
project is not successful unless
it is verified that all of the technical
specifications are fulfilled. The
way test facilities operate is subject
to constant change; the classical internal
combustion engine testbed is
evolving into an electrified one.
Today’s chassis dynamometers are
used not only for ICE vehicles but
for all kinds of electrical drive systems
too. But if an overall planner
has no practical experience in test facility
operation to fall back on, his
efforts will result in a non-functional
layout, in poorly thought out procedures
and, ultimately, in a higher total
cost of ownership. Here at AVL we
are constantly moving forward. Until
recently, I would still have mentioned
the Stuttgart Tech Center as an example
of best practice. Right now we are
building a new Tech Center in Coventry,
2 4 F O C U S
England. For the first time ever
in a Tech Center, we have installed vehicle
powertrain testbeds, 108 sq.m.
in size (l x w: 12 m x 9 m), in flexible
container modules. The container
modules were pre-assembled at one
of our locations and then transported
to England by truck. The technical
building facilities are installed in
40-ft ISO containers. With this concept
we can erect a complete Tech
Center in just 12 months and are also
capable of shifting the powertrain
containers to another location. When
we planned the workshops and testbeds
in the course of this project, we
focused on novel technologies – for
example virtual-reality glasses – and
gained some revolutionary perspectives
and experiences which were also
highly appreciated by the craftsmen.
>
Implementation of complete
vehicle powertrain testbeds
in new container module design
at the Coventry Tech Center
» HERE AT AVL WE
HAVE ALL THE TECHNICAL
CAPABILITIES
NEEDED TO MEET THE
OEMS’ REQUIREMENTS «
URS GERSPACH,
Executive Vice President Test Systems
and Global Operations