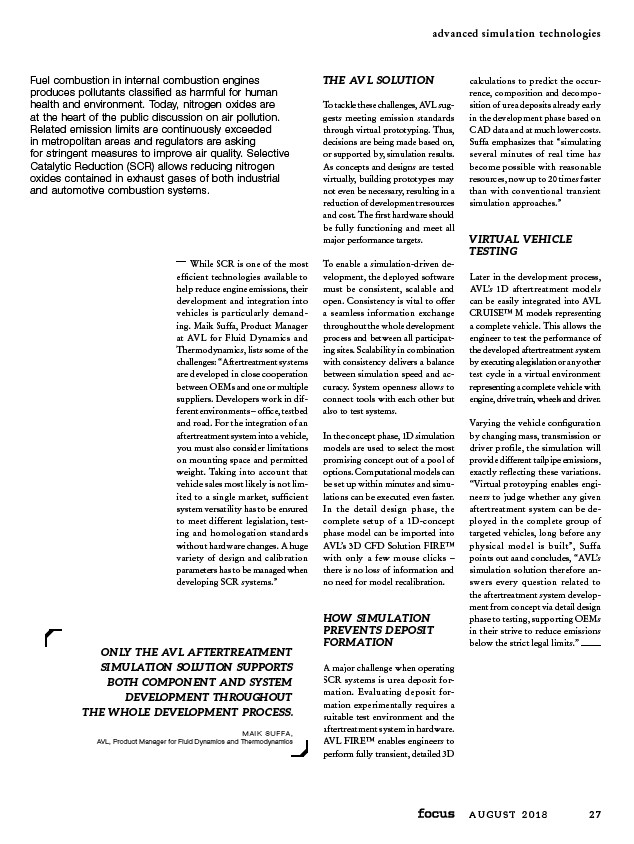
advanced simulation technologies
A U G U S T 2 0 1 8 2 7
THE AVL SOLUTION
To tackle these challenges, AVL suggests
meeting emission standards
through virtual prototyping. Thus,
decisions are being made based on,
or supported by, simulation results.
As concepts and designs are tested
virtually, building prototypes may
not even be necessary, resulting in a
reduction of development resources
and cost. The first hardware should
be fully functioning and meet all
major performance targets.
To enable a simulation-driven development,
the deployed software
must be consistent, scalable and
open. Consistency is vital to offer
a seamless information exchange
throughout the whole development
process and between all participating
sites. Scalability in combination
with consistency delivers a balance
between simulation speed and accuracy.
System openness allows to
connect tools with each other but
also to test systems.
In the concept phase, 1D simulation
models are used to select the most
promising concept out of a pool of
options. Computational models can
be set up within minutes and simulations
can be executed even faster.
In the detail design phase, the
complete setup of a 1D-concept
phase model can be imported into
AVL’s 3D CFD Solution FIRE™
with only a few mouse clicks –
there is no loss of information and
no need for model recalibration.
HOW SIMULATION
PREVENTS DEPOSIT
FORMATION
A major challenge when operating
SCR systems is urea deposit formation.
Evaluating deposit formation
experimentally requires a
suitable test environment and the
aftertreatment system in hardware.
AVL FIRE™ enables engineers to
perform fully transient, detailed 3D
calculations to predict the occurrence,
composition and decomposition
of urea deposits already early
in the development phase based on
CAD data and at much lower costs.
Suffa emphasizes that “simulating
several minutes of real time has
become possible with reasonable
resources, now up to 20 times faster
than with conventional transient
simulation approaches.”
VIRTUAL VEHICLE
TESTING
Later in the development process,
AVL’s 1D aftertreatment models
can be easily integrated into AVL
CRUISE™ M models representing
a complete vehicle. This allows the
engineer to test the performance of
the developed aftertreatment system
by executing a legislation or any other
test cycle in a virtual environment
representing a complete vehicle with
engine, drive train, wheels and driver.
Varying the vehicle configuration
by changing mass, transmission or
driver profile, the simulation will
provide different tailpipe emissions,
exactly reflecting these variations.
“Virtual protoyping enables engineers
to judge whether any given
aftertreatment system can be deployed
in the complete group of
targeted vehicles, long before any
physical model is built”, Suffa
points out aand concludes, “AVL’s
simulation solution therefore answers
every question related to
the aftertreatment system development
from concept via detail design
phase to testing, supporting OEMs
in their strive to reduce emissions
Fuel combustion in internal combustion engines
produces pollutants classified as harmful for human
health and environment. Today, nitrogen oxides are
at the heart of the public discussion on air pollution.
Related emission limits are continuously exceeded
in metropolitan areas and regulators are asking
for stringent measures to improve air quality. Selective
Catalytic Reduction (SCR) allows reducing nitrogen
oxides contained in exhaust gases of both industrial
and automotive combustion systems.
While SCR is one of the most
efficient technologies available to
help reduce engine emissions, their
development and integration into
vehicles is particularly demanding.
Maik Suffa, Product Manager
at AVL for Fluid Dynamics and
Thermodynamics, lists some of the
challenges: “Aftertreatment systems
are developed in close cooperation
between OEMs and one or multiple
suppliers. Developers work in different
environments – office, testbed
and road. For the integration of an
aftertreatment system into a vehicle,
you must also consider limitations
on mounting space and permitted
weight. Taking into account that
vehicle sales most likely is not limited
to a single market, sufficient
system versatility has to be ensured
to meet different legislation, testing
and homologation standards
without hardware changes. A huge
variety of design and calibration
parameters has to be managed when
developing SCR systems.”
ONLY THE AVL AFTERTREATMENT below the strict legal limits.”
SIMULATION SOLUTION SUPPORTS
BOTH COMPONENT AND SYSTEM
ONLY THE AVL AFTERTREATMENT
SIMULATION SOLUTION SUPPORTS
BOTH COMPONENT AND SYSTEM
DEVELOPMENT THROUGHOUT
DEVELOPMENT THROUGHOUT
THE WHOLE DEVELOPMENT PROCESS.
THE WHOLE DEVELOPMENT PROCESS.
MAIK SUFFA ,
MAIK SUFFA ,
AVL, Product Manager for Fluid Dynamics
AVL, Product Manager for Fluid Dynamics and Thermodynamics