Entwicklung von PEM-Elektrolyseuren unterstützt durch Multiphysik-Systemsimulation
Published on Juli 15, 2025 · 17 min read
Im vergangenen Jahr ist die weltweite Elektrolysekapazität um etwa 60 % auf 1,75 GW installierte Leistung gestiegen. Alkalische Elektrolyseure dominieren weiterhin den Markt und machen den Großteil dieser Kapazität aus, insbesondere in China. PEM-Elektrolyseure sind jedoch auf dem Vormarsch, insbesondere in Europa und Nordamerika, wo sie inzwischen einen erheblichen Anteil ausmachen.
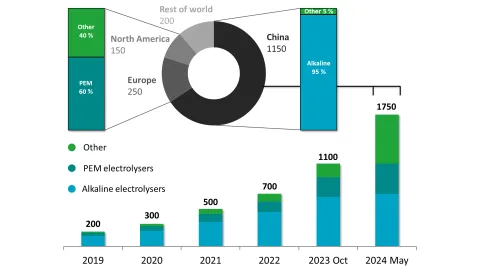
Die Hauptvorteile von PEM-Elektrolyseuren sind die hohe Dynamik, die erzielbare Leistungsdichte und der Betrieb bei niedrigen Temperaturen, was sie ideal für die Integration in erneuerbare Energiesysteme macht. Ihre hohe Stromdichte, die präzise Steuerbarkeit und der modulare Aufbau unterstützen sowohl den skalierbaren industriellen Einsatz als auch dezentrale Energiesysteme. Trotz der vielversprechenden Fähigkeiten von PEM-Systemen sind Entwurf, Prüfung und Optimierung von Elektrolyseur-Konfigurationen nach wie vor schwierig und ressourcenintensiv, vor allem wenn sie für industrielle Anwendungen skaliert werden sollen. Fortgeschrittene Simulationsmethoden haben sich als vielversprechende Lösung für diese Herausforderungen erwiesen und ermöglichen es Forschern und Ingenieuren, komplexe elektrochemische und thermodynamische Wechselwirkungen genau zu modellieren.
In diesem Artikel zeigen wir, wie AVL die Systemsimulation im Entwicklungsprozess für Design, Integration und Validierung eines PEM-Elektrolyseursystems einsetzt. Der Simulationsrahmen wurde anhand von experimentellen Daten aus der Literatur rigoros validiert, um sicherzustellen, dass das Modell das reale Verhalten zuverlässig widerspiegelt und die Dynamik des Massen- und Wärmetransports sowie die elektrochemischen Prozesse im Detail erfasst. Das Modell wurde eingesetzt, um seine Anwendbarkeit in verschiedenen Phasen des Entwicklungsprozesses zu demonstrieren, beginnend mit dem Konzeptentwurf und der Dimensionierung der Komponenten, gefolgt von der Entwicklung von Steuerfunktionen für verschiedene instationäre Betriebsszenarien.
Die Generierung des PEM-Elektrolyseur-Modells und die Berechnungen wurden in der modularen Systemsimulationsplattform AVL CRUISE™ M durchgeführt. Das untersuchte Gesamtsystem ist dem von Stansberry und Brouwer [2] beschriebenen System sehr ähnlich, allerdings sind in diesem Modell zusätzliche Änderungen enthalten. Das System ist für die Produktion von Wasserstoff zur Einspeisung in eine Erdgaspipeline bei einem Druck von 70 bar ausgelegt, mit einer maximalen Produktionsrate von 1 kg/h und einer angestrebten Reinheit von 99,999 %. Der PEM-Elektrolyseur-Stapel besteht aus 66 Zellen mit einer aktiven Fläche von 200 cm2.
Abbildung 2 zeigt das Modell des PEM-Elektrolyseur-Systems, wobei die wichtigsten Strömungspfade und Komponenten im Folgenden näher erläutert werden. Auf der Anodenseite gelangt das Wasser aus einem Tank in den O₂/Wasserabscheider, wobei der Durchfluss durch das Ventil 5 geregelt wird, um einen Flüssigkeitsanteil von 0,5 zu erhalten. Eine Pumpe leitet das Wasser über die Ventile 1 und 2 durch einen Entionisierungsfilter oder einen Bypass, gesteuert durch Leitfähigkeitssensoren. Während der Aufwärmphase fließt der gesamte Massenstrom durch einen Heizer, um die Zieltemperatur zu erreichen, ab der die Elektrolyse beginnt. Die Heizung wird dann über die Ventile 3 und 4 und die Pumpendrehzahl gesteuert, um das thermische Gleichgewicht zu erhalten. Der Sauerstoff wird im Separator gesammelt und bei 1,1 bar freigesetzt, wobei die Drossel 1 den Druck für den Hochdruckbetrieb regelt.
Auf der Kathodenseite wird der Wasserstoff im H₂/Wasserabscheider I von Wasser getrennt, vorgewärmt, um Kondensation zu vermeiden, und durch einen DeOxo-Katalysator geleitet, um Restsauerstoff zu entfernen. Ein Kondensator entfernt den Wasserdampf, wobei das kondensierte Wasser über das Ventil 7 zurückgeführt wird. Der Wasserstoff erreicht eine Reinheit von 99,9 % bzw. bis zu 99,999 % mit zusätzlicher PSA-Reinigung und wird auf 70 bar verdichtet. Beim Anfahren sorgt eine Stickstoffspülung für eine inerte Umgebung vor der Elektrolyse.
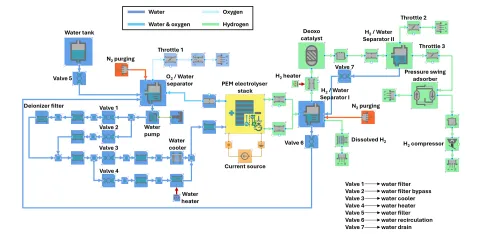
Das Systemmodell wurde anhand der Daten von Stansberry und Brouwer validiert, und die Simulationsergebnisse mit den Referenzdaten verglichen. In allen Fällen wurde eine gute Übereinstimmung zwischen den simulierten und den referenzierten Ergebnissen festgestellt, wobei nur geringfügige Abweichungen aufgrund von Unsicherheiten bei der Zellen- und Stapelgeometrie, dem Alterungszustand der Komponenten und Variationen der Betriebsbedingungen auftraten (Abbildung 3). Zusätzliche Faktoren, wie potenzielle Messungenauigkeiten und Schwankungen der Katalysatoraktivität, können ebenfalls dazu beigetragen haben.
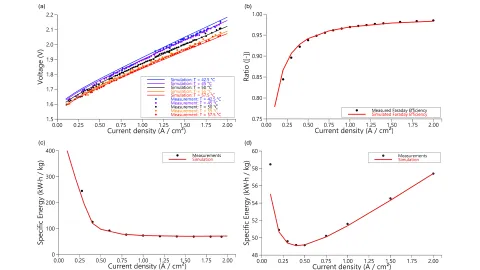
Das Modell wurde verwendet, um seine Anwendbarkeit in verschiedenen Phasen des Entwicklungsprozesses zu demonstrieren, beginnend mit dem Konzeptentwurf und der Komponentendimensionierung, gefolgt von der Entwicklung von Steuerfunktionen für verschiedene transiente Betriebsszenarien. Ausgewählte Anwendungsfälle werden im Folgenden detailliert beschrieben: Transientes Anfahren, Lastwechsel und Hot-Standby-Betrieb.
Transienter Start-up-Prozess
Die Entwicklung und Kalibrierung von Steuerungsfunktionen in einer virtuellen Umgebung ist ein entscheidender Schritt, um den Entwurf in einem frühen Stadium zu beschleunigen, den Bedarf an teuren Tests zu verringern und das physische System vor möglichen Schäden zu bewahren. Während die Regelungsstrategien für den stationären Betrieb relativ einfach sind, ist die Implementierung der instationären Regelung, insbesondere für Prozesse wie das Aufwärmen, aufgrund der langen Zeiträume eine Herausforderung. Die Simulation ermöglicht ein umfassendes virtuelles Testen und Verfeinern dieser Regelungsalgorithmen, was einen nahtloseren Übergang zum realen Betrieb ermöglicht und gleichzeitig die Systemstabilität und Gesamteffizienz verbessert.
Der in dieser Studie verwendete Aufwärmprozess besteht aus fünf Stufen (Abbildung 4). In der ersten Stufe werden sowohl die Anoden- als auch die Kathodenseite des Systems mit Stickstoffgas gespült, wodurch sichergestellt wird, dass sich auf der Kathodenseite kein Restsauerstoff und auf der Anodenseite kein Wasserstoff befindet. Dies ist sowohl für die Sicherheit als auch für die Systemleistung von entscheidender Bedeutung, da das Vorhandensein von Restgasen zu unkontrollierten Nebenreaktionen, Effizienzverlusten und vor allem zur Bildung eines explosiven H2/O2-Gemischs im System führen kann. Der nächste Schritt besteht darin, ein Wasserdurchflusssystem einzurichten, das eine Pumpe und einen Entionisierer umfasst. Die Entionisierung ist ein notwendiger Schritt, um potenzielle ionische Verunreinigungen zu entfernen, die von Quellen wie Rohren, Tanks oder anderen Systemkomponenten stammen können.
In der dritten Stufe wird die Heizung aktiviert, um die Wassertemperatur auf der Anodenseite allmählich zu erhöhen, wobei Temperaturgradienten berücksichtigt werden, um eine kontrollierte Erwärmung zu gewährleisten. Darauf folgt der vierte Schritt, in dem die elektrisch unterstützte Aufwärmphase mit Teillastbetrieb startet. Wenn die Elektrolyse beginnt, führt die exotherme Natur der Reaktion zu einem schnellen Anstieg der Kathodentemperatur. Sobald das System im fünften und letzten Schritt die angestrebte Betriebstemperatur erreicht hat, wird die Heizung deaktiviert und der Strom schrittweise auf Volllast erhöht. In dieser Phase wird die thermische Stabilität durch eine aktive Kühlung aufrechterhalten, was eine präzise Temperaturregelung des Wasserstroms gewährleistet. Die Volllast-Wasserstoffproduktion wird fast unmittelbar nach dem Umschalten auf Modus 5 erreicht (ca. 7 Minuten), während der thermodynamische Gleichgewichtszustand nach 14 Minuten erreicht wird, was das Ende der Aufwärmsequenz markiert.
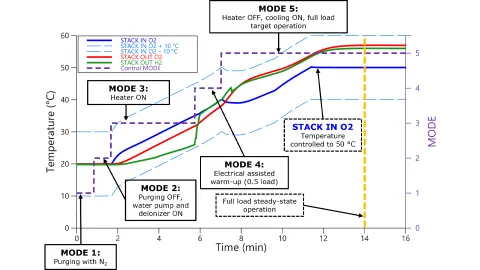
Lastwechsel
Zuverlässige Lastwechselvorgänge in PEM-Elektrolyseuren sind für die Systemstabilität, den Wirkungsgrad und die Haltbarkeit unter instationären Bedingungen von entscheidender Bedeutung, insbesondere im Zusammenhang mit der durch erneuerbare Energien betriebenen Wasserstoffproduktion. Da die Stromzufuhr aufgrund der Variabilität von Wind- und Sonnenenergie schwankt, ist das Verständnis der dynamischen Reaktion des Elektrolyseurs entscheidend für die Aufrechterhaltung der Leistung und die Vermeidung von Betriebsinstabilitäten (Abbildung 5).
In dieser Studie wurde die Betriebslast des PEM-Elektrolyseurs systematisch auf eine untere Lastgrenze von 25 % für eine Dauer von 250 Sekunden reduziert, bevor er wieder unter Volllastbedingungen betrieben wurde. Nach der Lastreduzierung verringerte sich die Elektrolyserate proportional, was zu einem deutlichen Rückgang der Wärmeerzeugung im Stack führte. Diese Verringerung der Wärmeleistung führte zu einem Rückgang der Anodenaustrittstemperatur von 55 °C auf etwa 51 °C. Bemerkenswert ist, dass die Stackeintrittstemperatur auf der Anodenseite durch eine präzise Ventilsteuerung konstant bei 50 °C gehalten werden kann. Der Unterschied zwischen der Stack-Eintritts- und -Austritts-Temperatur an der Anode wird auch indirekt durch den Wasserfluss durch den Stack gesteuert. Im Volllastbetrieb arbeitet die Wasserpumpe mit Nenndrehzahl, wodurch die Stack-Temperaturdifferenz von 5 °C aufrechterhalten wird.
Durch die Verringerung der Geschwindigkeit der Wasserpumpe wird die Durchflussmenge durch den Stack verringert, wodurch sich die Verweilzeit des Wassers im Stack verlängert. Durch diese verlängerte Verweildauer kann das Wasser mehr Wärme aufnehmen, die während des Betriebs erzeugt wird, was zu einer höheren Austrittstemperatur führt. Durch die Verringerung der Belastung des PEM-Elektrolyseurs wird der durch das System fließende Strom gesenkt, was zu einer erheblichen Verringerung der Wärmeerzeugung im Stack führt.
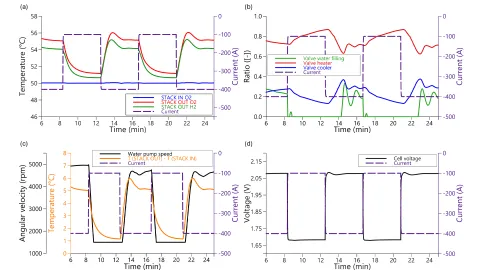
Diese verringerte Wärmeleistung reduziert die Notwendigkeit einer aktiven Kühlung und ermöglicht ein passives Wärmemanagementkonzept. Die Beibehaltung des vom Stack-Lieferanten angegebenen Mindestwasserdurchflusses führt jedoch zu einer Stack-Temperaturdifferenz von etwa 1 °C. Gleichzeitig korreliert der Rückgang des Stroms mit einem Anstieg der Zellenspannung, die von etwa 1,7 V bei 25 % Last auf fast 2,1 V bei Volllast ansteigt.
Hot-Stand-by Betrieb
Der Hot-Standby-Betrieb ist eine der wichtigsten Betriebsarten für PEM-Elektrolyseure, insbesondere wenn versucht wird, die LCOH (Levelized Cost of Hydrogen) zusammen mit variablen erneuerbaren Energiequellen zu optimieren. In diesem Modus hält der Elektrolyseur seine Betriebstemperatur und seinen Betriebsdruck aufrecht, ohne Wasserstoff zu produzieren, was eine schnelle Wiederaufnahme des vollen Betriebs innerhalb von Sekunden ermöglicht. Durch diesen Bereitschaftsbetrieb werden thermische Zyklen minimiert, die die Systemkomponenten beeinträchtigen und die Lebensdauer verkürzen können. Darüber hinaus wird der Energieverbrauch im Vergleich zu einer vollständigen Abschaltung gesenkt, da die für das Wiederaufheizen erforderliche Energiemenge vermieden wird, was insbesondere dann von Vorteil ist, wenn der Betrieb des Systems nach einer kurzen Ausfallzeit wieder aufgenommen wird.
Das virtuelle Hot-Standby-Experiment beginnt damit, dass der PEM-Stack auf seinen Volllast-Sollwert gebracht wird, wobei der Strom konstant gehalten wird, um die Zelle auf 50 °C zu erhitzen. Bei t = 10 min wird der Strom auf Null reduziert, wodurch die Elektrolyse sofort gestoppt und die Erwärmung des Speisewassers verhindert wird. Da die konduktiven und konvektiven Verluste die Stack-Austrittstemperatur nach unten treiben, wird die Zusatzheizung eingeschaltet und das Kühlventil (Ventil 3) schrittweise geschlossen. Die Heizleistung steigt rasch an und konvergiert auf etwa 0,7 kW, wodurch die systemeigenen Wärmeverluste genau ausgeglichen werden und der Sollwert von 50 °C aufrechterhalten wird (Abbildung 6).
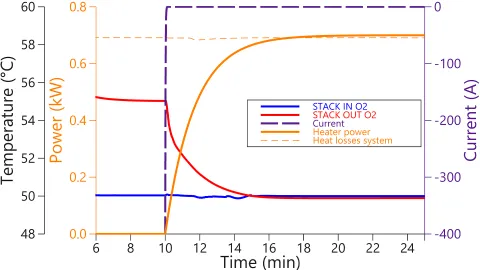
Durch die Vermeidung einer vollständigen Abschaltung minimiert die Hot-Standby-Strategie die thermische Beanspruchung der Membran und der Katalysatorschichten, erhält die Haltbarkeit der Komponenten und ermöglicht eine nahezu sofortige Rückkehr zur Elektrolyse, sobald der Strom wieder angelegt wird.
Der PEMEL-Stack-Wizard
Die Simulationssoftware AVL CRUISE™ M bietet eine breite Palette von Modellfunktionen und Simulationsmöglichkeiten, einschließlich eines PEMEL-Wizards, der die Modellierung und Parametrisierung des Stackmodells vereinfacht. Mit seinem geführten Arbeitsablauf werden die Benutzer durch einen strukturierten und intuitiven Prozess unterstützt, um ihre Stack-Modelle entweder mit stationären oder transienten Messdaten zu kalibrieren. Die benutzerfreundliche Schnittstelle fügt sich nahtlos in die bestehende PEMEL-Stack-Komponente ein, was den Zugang erleichtert und eine reibungslose Übertragung der Parameter gewährleistet.
Der Wizard ermöglicht die Optimierung von Parametern für bis zu 14 auswählbare Eingaben und ermöglicht so eine flexible und präzise Kalibrierung, die auf den Datensatz des Benutzers zugeschnitten ist. Zur Unterstützung der Modellvalidierung und -abstimmung bietet das Tool auch eine erweiterte Analyse der Ergebnisse, einschließlich Paritätsdiagrammen und Polarisationskurven, die einen unmittelbaren Einblick in die Qualität der Anpassung und das Modellverhalten geben. Diese Funktionalität ermöglicht es Ingenieuren, genaue, originalgetreue PEMEL-Modelle effizienter zu entwickeln, und ebnet den Weg für schnellere Innovationen in der Wasserstofftechnologie.
Der PEMEL-System-Generator
Eine der größten Herausforderungen im aktuellen Kontext ist das Fehlen etablierter Modellierungsmethoden ein Umstand, der oft durch die unvollständige Verfügbarkeit™ von Komponentendaten noch verschärft wird.
Um dieses Problem zu lösen, haben wir den PEMEL-System-Generator entwickelt, der eine konsistente, skalierbare Modellierung von PRM-Elektrolyse-Systemmodellen ermöglicht und den Aufwand für deren Erstellung minimiert (Abbildung 7).
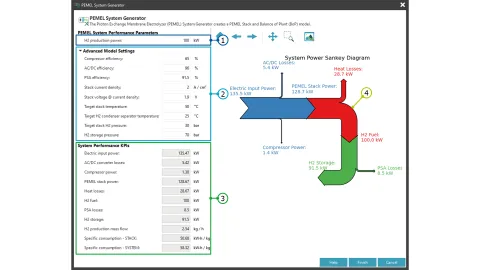
- H2-Produktionsleistung: Der Generator beginnt mit einer einfachen Eingabe: der angestrebten Wasserstoffproduktionsleistung (basierend auf dem oberen Heizwert). Diese dient als primärer Parameter für die Erstellung des kompletten Systemlayouts, einschließlich der entsprechenden Skalierung der Komponenten.
Erweiterte Modelleinstellungen: Der Benutzer hat die Möglichkeit, die Systemleistung zu beeinflussen, indem er die Wirkungsgrade für die wichtigsten Komponenten festlegt:
a) Wirkungsgrad des Verdichters: Dieser Wert bezieht sich auf den Wasserstoffkompressor, der den Wasserstoff vom Betriebsdruck des Systems auf den Speicherdruck verdichtet. Ein höherer Wirkungsgrad reduziert den Stromverbrauch des Kompressors.
b) AC/DC-Wandler-Wirkungsgrad: Da der PEM-Elektrolyseur-Stapel (PEMEL) Gleichspannung benötigt und typische Netzanschlüsse Wechselspannung liefern, ist ein AC/DC-Wandler erforderlich. Sein Wirkungsgrad bestimmt den Hilfsleistungsverlust während der Umwandlung.
c) PSA-Wirkungsgrad: Während des Wasserstoffreinigungsprozesses stellt die Trocknung eine große Herausforderung dar. Um die erforderliche Wasserstoffreinheit zu erreichen, müssen Druckwechselabsorber (engl. Pressure-Swing-Absorber PSA) oder Temperaturwechselabsorber (engl. Temperature-Swing-Absorber TSA) eingesetzt werden, die beide erhebliche Energieverluste verursachen.
d) Stack-Betriebspunkt: Das System ist für den Betrieb an einem nominalen Volllastpunkt ausgelegt, der in der Regel durch die Eigenschaften des Stacks definiert ist. Der Benutzer kann die "Stack-Stromdichte" und die entsprechende "Stack-Spannung" vorgeben, was eine automatische Feinabstimmung der elektrochemischen Parameter für eine genaue Stack-Modellierung ermöglicht.
e) Randbedingungen: Die letzten vier Eingaben ermöglichen die Kontrolle über die Randbedingungen im System. Dazu gehören:
- Einlasstemperatur des Stack-Kühlmittels
- Kondensatortemperatur in der ersten Stufe der Wasserstofftrocknung
- Betriebsdruck des Systems
- Wasserstoffspeicherdruck
KPIs: Die schnelle Berechnung der wichtigsten Leistungsindikatoren gibt einen klaren Überblick über die Effizienz des Systems. Diese KPIs umfassen:
- Leistungsbilanzen der einzelnen Komponenten
- Wasserstoff-Massendurchsatz
- Spezifischer Energieverbrauch des Stacks und des gesamten Systems
- Sankey-Diagramm: Um die Leistungsbilanzen im System visuell darzustellen, wird ein Sankey-Diagramm verwendet. Dieses bietet einen klaren und intuitiven Überblick über die Energieverteilung und die Verluste im gesamten System.
Sobald der Benutzer alle erforderlichen Eingaben getätigt hat und die wichtigsten Leistungsindikatoren (wie im Sankey-Diagramm dargestellt) als akzeptabel und plausibel erachtet werden, kann das Systemmodell durch Anwählen der Schaltfläche „Fertig stellen“ generiert werden. Das resultierende Layout wird als Anfangskonfiguration festgelegt und dient als optimaler Ausgangspunkt für jeden Benutzer. Weitere Modifikationen der Systemarchitektur sind einfach möglich und können je nach den spezifischen Bedürfnissen oder Optimierungszielen vorgenommen werden.
Das erstellte Modell besteht aus drei Hauptabschnitten:
Die Komponenten Stack und Balance of Plant (BoP) stellen die physische Hardware des Gesamtsystems dar, in dem thermodynamische und elektrochemische Berechnungen durchgeführt werden. Ihre Konfiguration ähnelt stark dem im ersten Teil dieses Blogs beschriebenen System.
Steuerungskomponenten spielen eine entscheidende Rolle im System, indem sie Pumpen, Ventile und Kompressoren regulieren, um die gewünschten Betriebsbedingungen aufrechtzuerhalten. Diese Komponenten sorgen dafür, dass das System effizient funktioniert und innerhalb der festgelegten Parameter bleibt.
- Alle physikalischen Größen wie Druck, Temperatur, Massenströme und elektrochemische Parameter sowie andere wichtige Leistungsindikatoren (KPIs) werden an die Monitor-Komponenten weitergeleitet (Abbildung 8). Dies ermöglicht eine Echtzeitbeobachtung über eine umfassende Online-Monitoring-Schnittstelle, die alle wichtigen Systeminformationen auf einen Blick liefert. Darüber hinaus umfasst das Setup eine Konvergenzkontrollkomponente, die anzeigt, ob das System einen stabilen Betriebspunkt erreicht hat, um sicherzustellen, dass die Simulationsergebnisse zuverlässig sind.
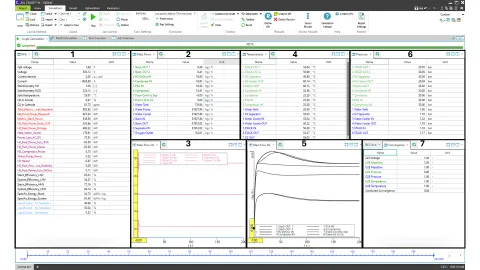
Dieser Artikel zeigt, dass die fortschrittliche dynamische Modellierung eines PEM-Elektrolyseurs nicht nur die wichtigsten experimentellen Leistungskennzahlen mit hoher Genauigkeit wiedergibt, sondern auch wertvolle Einblicke in den dynamischen Betrieb, die Entwicklung von Kontrollstrategien und Überlegungen zur langfristigen Haltbarkeit bietet. Durch eine strenge Validierung anhand von Literaturdaten erweisen sich die entwickelten Modelle als geeignet für eine breite Palette von Anwendungsfällen in verschiedenen Phasen des Entwicklungszyklus. Die Einbeziehung von Alterungseffekten, wie z. B. nachlassende Stack-Leistung und erhöhter Wasserstoff-Crossover, unterstreicht die kritischen Sicherheits- und Leistungsabwägungen zwischen Betriebsstromdichte und Langlebigkeit der Komponenten, die z. B. für LCOH wichtig sind.
Durch die Erfassung des gesamten Spektrums des instationären Verhaltens bietet das Modell eine robuste Grundlage für die Untersuchung dynamischer Phänomene, die bei stationären Analysen oft übersehen werden. Dazu gehören Szenarien wie Aufwärmphasen, Lastübergänge und Hot-Standby-Betrieb, die als repräsentative transiente Fälle demonstriert wurden. Durch die Identifizierung optimaler Betriebszustände, die ein Gleichgewicht zwischen Effizienz, Langlebigkeit und Sicherheit herstellen, dient der vorgestellte Rahmen als leistungsstarke Methodik zur Beschleunigung der Entwicklung, des Scale-up und der kosteneffizienten Einführung zuverlässiger PEM-Elektrolysesysteme für die Integration in eine auf erneuerbaren Energien basierende Wasserstoffinfrastruktur.
Literatur
[1] M. &. Company, “Hydrogen Insights September 2024,” Hydrogen Council, 2024.
[2] J. M. Stansberry and J. Brouwer, “Experimental dynamic dispatch of a 60 kW proton exchange membrane electrolyzer in power-to-gas application,” Int. J. Hydrogen Energy, 45, 9305-9316, 2020.
Stay tuned
Don't miss the Simulation blog series. Sign up today and stay informed!
Stay tuned for the Simulation Blog
Don't miss the Simulation blog series. Sign up today and stay informed!