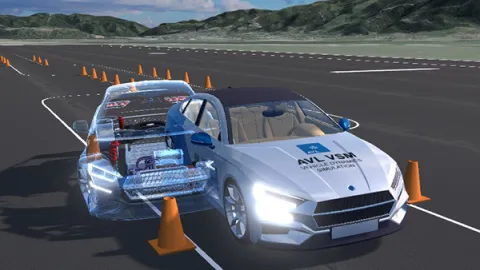
The electrification of the powertrain has been one of the technological highlights in vehicle development over the last few years. The common multi-electric-machine topologies cost-effectively enable powertrain functions like all-wheel-drive (AWD) or torque vectoring. While a standard powertrain requires complex gearboxes to divert drive torque towards the wheels, electric powertrains can handle this task in most cases without any additional mechanical gear. Maximizing the benefit of the e-AWD powertrain requires the extension of control function development. Effective development of controls tailored to a specific powertrain topology and vehicle combination must follow a strict functional development process. AVL has established an approach for the functional development of e-AWD and torque vectoring controls that starts very early in the development timeline. AVL VSM™ and AVL-DRIVE™ are used as tools for Model-in-the-Loop (MiL) simulation and assessment. This enables AVL to define the e-AWD functions and identify the optimum hardware characteristics and required control algorithms by balancing performance, vehicle dynamics and efficiency. The ultimate goal is to create a perfect match of the requirements set in the vehicle’s customer market profile sheet. With MiL simulation, the controls can be virtually calibrated before being transferred to a real hardware ECU as software code, enabling the in-vehicle calibration to start on a more mature level, and helping to save time and development costs. In this 60-minute webinar, Joachim Ecker, Technical Expert Chassis, outlines how the AVL e-AWD development process ensures efficient and cost-effective controls development, and helps to optimize powertrain functions and vehicle dynamics.
Watch now
Meet our experts who are the presenters of this webinar.