Under current global legislation, vehicles must not exceed prescribed emission levels. Hybrid electric vehicles are one possibility to meet these legislative requirements. However, hybrid powertrain systems are very complex and traditionally, the performance of the engine, transmission, aftertreatment and e-drive systems are evaluated and often optimized separately by different departments. Testing is expensive and the multi-dimensional nature of the problem makes optimizing the whole system nearly impossible for engineers. Additionally, the development of hybrid electric vehicles requires a lot of testing resources, that might not be available. Most of the system testing is done on powertrain testbeds, which are complex to operate and very cost intensive.

In AVL, we uncovered the many resource conflicts and successfully transformed an existing internal combustion engine testbed into a hybrid vehicle test environment. Specifically this means, we have made it possible to use engine testbeds, as if they were powertrain testbeds. How does this upgrade work? We are bringing simulation to the testbed. The complete solution consists of a real-time execution platform, the necessary virtual components, and a commissioning tool to form a virtual pallet. As a last important part, we add preparation and execution tools, as it is necessary to bring the real-life cycles to the testbed, and, moreover, to efficiently execute the test plan using optimization software.
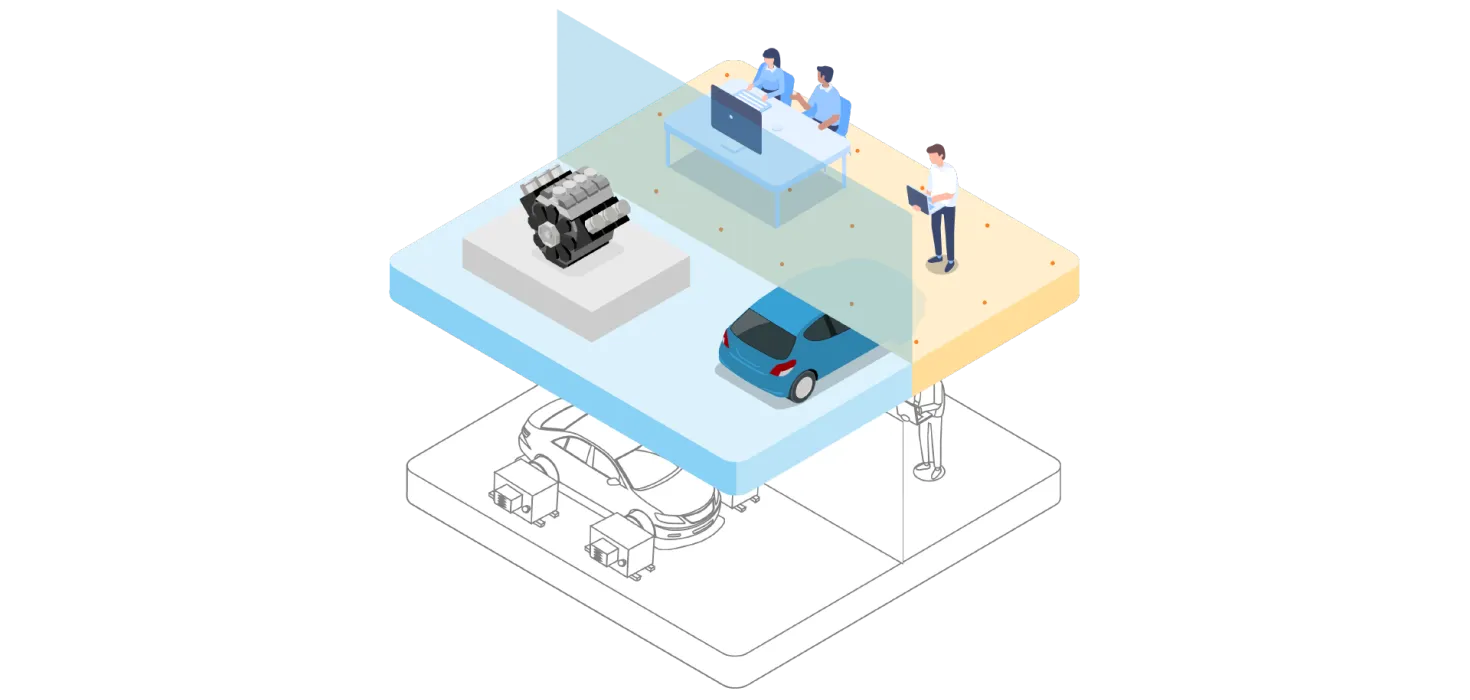
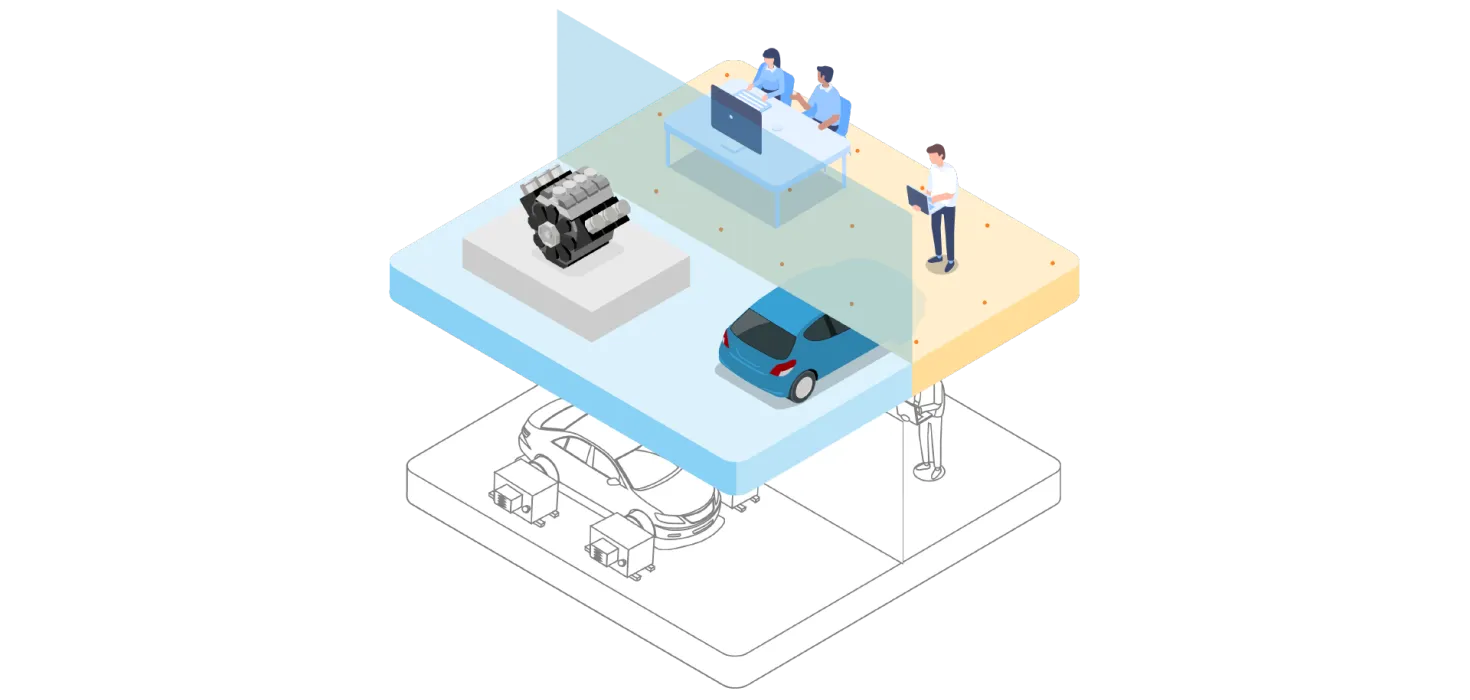
Increase testing resources
Maximum use of expensive test facilities, prototypes and models.
Lifetime extension
Extend the lifetime of your engine testbed and re-use it for hybrid electric vehicle development.
Seamless integration
Easily adapt the configuration of your testbed and integrate virtual components into the development ecosystem.
Real-Time Execution Platform
Allows that models, created in the office can be used at the testbed. With up to 10kHz of real-time execution, even the highly dynamic models e.g. for drivetrain and vehicle simulation, are properly executed. Our technology is open for implementing non-AVL vendor models.
Model Library
A modular and open model kit, compatible with office co-simulation environments and real-time execution platforms. Included are models for powertrain components, the driver, but also the testbed dyno and the unit under test (like the internal combustion engine).
Test Preparation and Execution
Preparation and execution tools, to bring real-life cycles to the testbed, and furthermore efficiently execute the test plan by using an optimization software.

Together with one of our customers, we recognized the resource conflict and jointly developed a solution to convert an engine testbed into a test environment for hybrid vehicles. Now this solution is available to all our customers and offers significant savings potential.
– Aleš Kolar, Senior Product Manager, Virtual Testing Solutions, AVL
Advanced Methodology for Hybrid Calibration at Hyundai Motor Europe Technical Center
We are constantly working on new solutions. The following might be interesting for you: