How to Improve the Quality of Results in Off-Road Testing
Published on February 24, 2025 · 2 min read
To achieve a high-fidelity vehicle simulation model, the vehicle is tested on a proving ground with specific maneuvers, initially using only the tarmac part. A Virtual Twin is then created using available inputs, such as vehicle dimensions, weight distribution, powertrain specifications and related maps, aero, chassis and suspension characteristics, brake and the tire model.
It is often the case that a vehicle is not available in the early stages because it is being used for other testing purposes, or some of the measurements and input data are missing. In these cases, a modelling approach based on user-defined KPIs is applied by setting the known vehicle performance results (e.g. acceleration time, braking distance). The model is automatically updated based on an artificial intelligence feature in VSM.
This feature is called vehicle model generation and uses an AI-based approach that is very powerful to automatically update vehicle parameters based on few performance inputs. This is very useful when real measurement data is incomplete, or in many cases at early stages when a real production, prototype or mule vehicle does not yet exist.
Maneuvers such as acceleration, braking, coast down, constant load, cornering (constant and transient), slalom, step steer, weave test are part of the matrix of test cases normally simulated in the VSM environment. By adapting the simulation model to real test results or user defined KPIs, the vehicle is finally ready and can be converted to off-road by changing the tire model.
Normally, vehicle models are not created directly for off-road conditions, as on-road test cases are easier to reproduce and repeat. However, there are exceptions: depending on the complexity of the off-road test case, it may be modelled directly in off-road conditions. In many cases, existing on-road models can be updated for off-road use.
To convert a model to off-road conditions, new soft soil and tire models are applied to the virtual vehicle, incorporating the tire design characteristics that can be measured directly from the tire tread pattern. There are several methods for set the off-road soil properties: the simplest approach is to use soil templates, with VSM offering a variety such as dirt roads, mud, sand, etc.
Alternatively, soil properties can be derived from real vehicle measurements taken during real off-road tests. Once some measurements are available, including different engine torque and wheel slip ratios, the soil properties can be "tuned" to match the test data.
Given that the tire design remains unchanged and the vehicle characteristics stay the same, the soil model can be easily optimized to align with the real-world data.
After repeating this step for different roads and soil types where the vehicle has been tested, the Virtual Twin is ready to be used for control development, calibration, tire selection and overall vehicle off-road performance optimization. These activities can be carried out in the office (SiL), on a testbed (HiL, ETB, PTTB) or using a driving simulator (DiL), with the same model being used in all environments.
Many simulation engineers reduce tire grip and increase resistance to virtually reproduce off-road test cases, a method that works well for low-friction surfaces like wet or icy tarmac conditions. However, this approach doesn’t fully capture the complex physics of real off-road conditions, such as the tire interaction with sand, dirt roads, mud or snow.
The additional resistance applied to the tires and the forces interaction differ significantly for off-road conditions. Not only are transient maneuvers affected, but steady-state behaviors also change, requiring more accurate simulations to reflect off-road conditions. These differences stem from the complex and dynamic nature of off-road surfaces, which vary in many properties.
Off-road soil and tire models work together and should account for phenomena such as bulldozing, where soil material is compressed and accumulated in front of and beside the tires, and the different interactions of front and rear tires with the soil due to the multi-pass effect, where the front wheels compact the soil before the rear wheels make contact.
By considering the previously mentioned phenomena, along with the soil properties and tire tread geometry, simulations can accurately predict the resulting resistance and force for each wheel, across various vehicle velocities and tire slip ratios. This enables more realistic performance analysis and optimization for off-road test cases, improving design and testing efficiency without the need for extensive real-world trials.
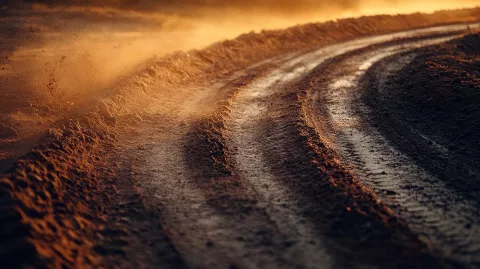
In off-road vehicle simulation, the soil properties are fundamental in determining the vehicle performance for different maneuvers. Accurate parameterization of these properties is crucial for the quality of the simulation results, including transient load conditions. To facilitate the workflow, several methods are available to obtain these properties:
- Use predefined soil templates, with VSM offering a variety such as dirt roads, mud, sand, etc.
- Extract them from real vehicle-level measurements taken during real off-road tests, using signals such as engine torque and wheel slip ratios, tuning the soil properties to match the test data.
In addition, the soil model can be refined by collecting tire-soil sinkage geometry data from the real proving ground. Soil samples can also be sent for laboratory analysis to further improve accuracy, although this is optional. In some cases, both the tire and the soil are tested on a test bench where the above methods are replicated in a controlled environment.
Correlating simulation results with real-world test measurements is the important final stage in validating and refining vehicle simulations, particularly for off-road performance. By comparing simulation results, such as vehicle and tire performance, with real data from a proving ground or test bench, engineers can ensure that the models accurately replicate the vehicle's behaviour in off-road conditions.
This correlation process typically involves replicating real driving maneuvers in a virtual environment, applying identical driver inputs to the simulation model. Critical parameters such as engine torque, wheel torque, and wheel speed are then analyzed. This systematic comparison helps minimize discrepancies between virtual and real-world tests, ensuring a reliable and highly realistic simulation.
Once the simulation model has been validated, it can be used for more advanced applications, such as optimizing the vehicle controls and calibration under various conditions without the need for extensive physical testing. Engineers can also explore different scenarios to refine vehicle systems or make decisions on new components such as tires, transmission components (e.g. differential) and strategy (e.g. torque split).
The integration of this simulation-based validation leads to an average reduction in development time of up to 50%. This has a significant impact on the costs associated with calibration, prototyping, and test drives. The VSM add-on provides a powerful and cost-effective solution for precise off-road simulation. The onboarding time for simulation engineers to work with VSM off-road test cases ranges from two to four days, depending on the environment – whether SiL, HiL, test benches, or driving simulators. This structured approach makes digital vehicle development not only more precise but also significantly more cost-efficient.
Stay tuned
Don't miss the Simulation blog series. Sign up today and stay informed!
Learn More About This Topic
Stay tuned for the Simulation Blog
Don't miss the Simulation blog series. Sign up today and stay informed!