How Simulation Helps the Marine Sector Become More Sustainable
Published on October 01, 2024 · 12 min read
The applicability of system simulation is found in three phases, encompassing both the development and operational aspects of the ship. In the concept and design phase, simulation is used to optimize the system through rigorous parameter studies, along with meeting engineering requirements and performing initial system optimization studies, concept comparison, identification of system requirements and boundary conditions for the domains. Finally, the operational aspect covers performance optimization, maintenance planning, bridge assistance systems, virtual sensors, and simulators. Here, the models can be used to support route optimization, performance enhancement, online monitoring, or to train engineers on simulators.
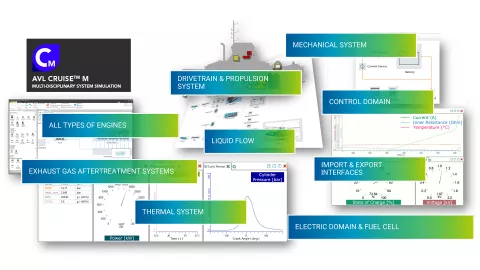
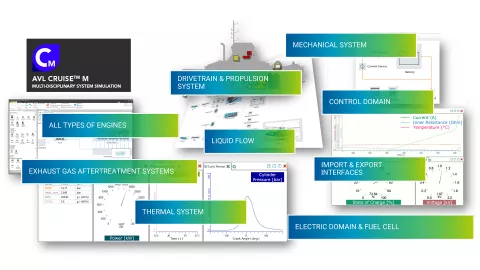
Main Building Blocks for the Digital Transformation in the Shipping Industry
Integrated simulation relies on digitalization even more than individual system simulation. The first predisposition includes accurate data acquisition, followed by data analytics that provide inputs for the following system simulation. The generation of digital and Virtual Twins is key to the simulation process, providing the engineer with a user-friendly interface and a complete overview. They propel model-based development and help users to visualize and work with the merged simulation blocks. Consequently, the simulation solution enables virtual testing in a virtual environment saves time and financial resources in the development of ships and in already existing models alike.
The Requirements for Simulation Software
The main requirement is a modular arrangement in the user interface, where each block represents a specific domain. Next, the simulation platform needs transient operating conditions and must allow the dynamic analysis of the ship and the study of the mutual interactions of its components and subsystems. The simulation software provides the level of detail required. All of this can be achieved with a comprehensive multi-domain and multi-physics computing platform.
In the following section we explore three use cases in which integration unlocks system level simulation. The simulation is enabled by a specifically developed toolchain powered by our solutions AVL CRUISE™ M and Model.CONNECT™. CRUISE M is a versatile simulation platform for fast and easy virtual analysis and optimization of systems, sub-systems and components. This solution is the core of the platform, enabling the creation of the models thanks to the several libraries available, able to cover the modelling of the relevant simulation domains.
Model.CONNECT is a co-simulation environment which allows connecting the specific sub-models and the overall one. As a result, components are viewed as a unified whole rather than as separate, non-communicating parts, making them ideal for a complex and large structure like ships. It is possible to integrate third-party tools in co-simulation (e.g. Simulink open models) and manage models easier. Usually, it is applied when a complex system simulation model is generated, and several engineering teams are responsible for the generation and maintenance of the sub-models to increase cooperation possibilities.
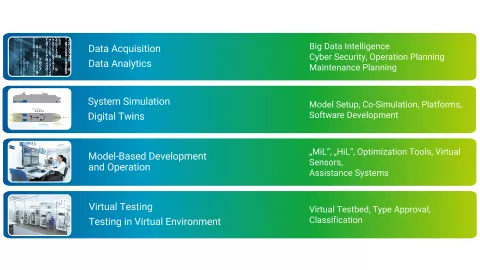
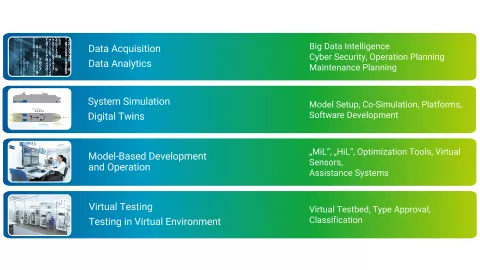
Use Case 1: Optimization of the Fuel Consumption With Real-Time Capable Engine Models
A ship’s fuel consumption depends on several factors, such as ship size, hull form, carrying capacity, vessel route, engine characteristic, and sailing speed. Despite the high fuel consumption in ships, it is not cost-effective to replace it with a more sustainable fuel. To illustrate, low-grade fuel would cost a large cruise ship 130,000$ a day for 80,000 gallons, whereas Marine Gas oil costs a ship whopping ~US $ 300,000/ day1.
It is also important to consider the costs linked to the engine development and testing. The usage of simulation can support the improvement of the engine design phase, the development and calibration of the ECU functions and the estimation of fuel consumption and NOx emissions in realistic working cycles. This can be done with CRUISE M 1D and 0D engine models. Having a large engine model on the HiL system can save millions in the development costs.
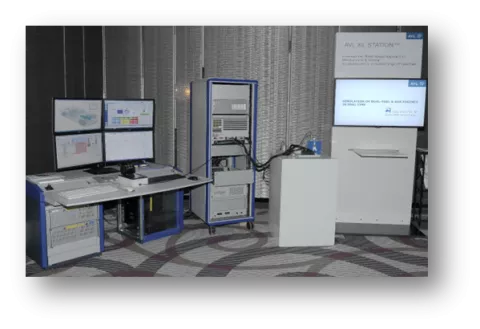
In a paper published in the 18th Symposium „Sustainable Mobility, Transport and Power Generation”2 a Virtual Twin of the propulsion and energy system of the vessel was created. Then the environmental impact was described. For this, empirical and semi-empirical emission models for N2, O2, CO2, NOX, HC and H2O were set up based on measured data. A crank-angle resolved engine model was created for model-based development, providing deeper insights into the engine through phenomenological combustion and emission models.
Later on, simplified map-based models were derived, allowing higher computational speed and are thus well suited for efficient simulation of entire voyages. This ship configuration allows for predicting instantaneous and cumulative emissions for a voyage, considering parameters like tonnage, ship resistance, and wind.
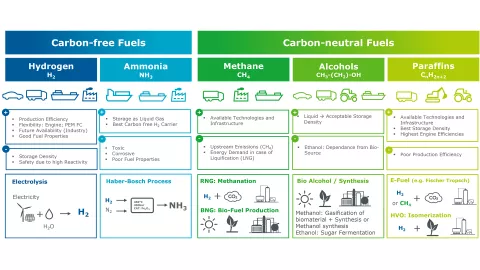
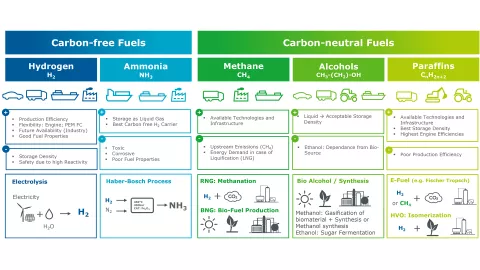
1 https://www.marineinsight.com/videos/video-how-much-fuel-does-a-cruise-ship-consume/
2 Source: paper “Evaluation of LNG as alternative fuel for large marine engines by means of predictive emission model”
Use Case 2: Simulation of Real-Life Ship Operations to Improve the Ship’s Efficiency
Onboard systems waste a lot of energy, primarily in the form of heat. This makes the analysis of real-world operation to implement effective on-board energy management a driving factor in reducing fuel consumption and its emissions. For example, the hotel loads can be covered by generating the energy from a genset or from a fuel cell (e.g. solid oxide fuel cell). In addition, the enthalpy contained in the exhaust gases or the heat rejected from the internal combustion engine could be used to warm up the pools or generate steam. The applications extend further using models like freshwater cooling systems, various water re-heating systems, and steam recovery systems.
Such a complex interaction results in varying fuel and energy consumptions dependent on several parameters. System simulation could therefore support the optimization of the ship control strategy in combination with a 3-DOF model of the ship itself. The Model Predictive Control algorithm can compute the rudder angle and the ship speed to reach target coordinates and ship orientation with discrete steps and minimized costs. A flexible approach to defining and weighting objectives through an optimization cost function, including travel time and energy or fuel consumption in combination with adequate ship dynamics model is the key to success. An example of this design can be seen in the following video.
Use Case 3: Supporting the Hybridization And Electrification Trend in the Marine Sector
As hybridization and electrification of ships is becoming increasingly important, CRUISE M offers the possibility to study hybrid and electrified concepts thanks to existing data for electric machines, fuel cells and batteries.
For example, several types of different models can be used for the description of the battery characteristics regarding chemical, electrical and thermal behavior as well as aging processes. These models can be divided into the main types of physical, empirical and abstract models. For the simulation on system level two different model types are available in CRUISE M.
The parameterization of the battery model is supported by the Battery Parameterization Wizard of CRUISE M. This tool calculates the model parameters from measured dynamic data for charging and discharging at different conditions.
Similarly, different sub-models and wizards are available for the analysis of fuel cells and the balance of plant. Both PEMFC (LT and HT) and SOFC stacks and balance of plant can be simulated. In the chart below, a standalone model of the fuel cell stack and the anode and cathode branches of the balance of plant is shown.
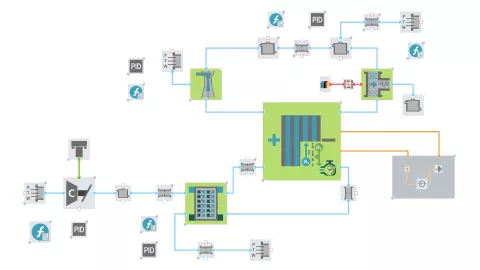
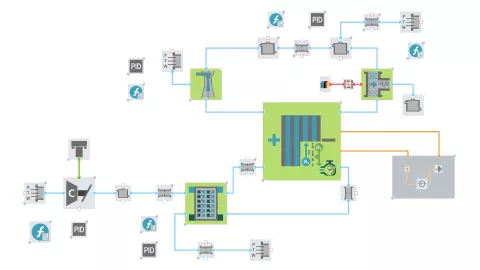
Overall, the marine sector will undergo massive changes in terms of saving resources and optimizing marine systems to meet stringent environmental targets. Our simulation solutions offer a transformative approach by allowing ships to be modeled as integrated systems rather than isolated components. This advancement is crucial for achieving the net-zero targets by 2050. Simulation software equips engineers with the tools to optimize entire ship systems, driving efficiency, reducing pollution, and minimizing emissions. Embracing virtualization will not only enhance operational performance but also contribute significantly to a more sustainable maritime industry.
To read more on sustainable maritime solutions, we recommend the paper "Modelling and Simulation of a Fully Electric Hybrid Propulsion System for Passenger Ships Using AVL CRUISE™ M Software". The paper explores the potential of hydrogen as a primary power source and analyses the system’s dynamics and performance using multi-physics simulation tool CRUISE M.
Stay tuned
Don't miss the Simulation blog series. Sign up today and stay informed!
Learn More About This Topic
Stay tuned for the Simulation Blog
Don't miss the Simulation blog series. Sign up today and stay informed!