This version of AVL CRUISE™ M facilitates the setup of comprehensive piping systems with a dedicated CAD Importer. When you start the CAD Importer from CRUISE M’s Efficiency Portal, SHAPE opens. It is a tool to import, clean and manipulate CAD data. In SHAPE, you can load the CAD data of your piping system and the tool automatically analyzes the geometry with respect to the needs of a CRUISE M model.
All identified components are enumerated on a dedicated staging list that allows you to inspect data, select/hide components as well as connect components to form bigger assemblies. Once this preparatory work is done, you have the option in an importing process to create the corresponding CRUISE M components only or, alternatively, equip each component additionally with Mass Flow and Pressure Termination components. This gives you a model that is ready to run, including pre-wired monitoring channels on mass flows, pressure losses, Reynolds number, etc. to get immediate feedback on the automatically created piping system.
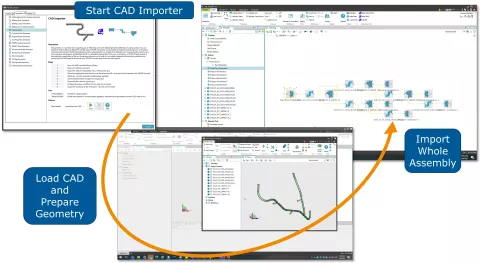
Multiport Extruded Tube (MPET) heat exchanger is often used in refrigerant circuits to serve as a condenser or evaporator. CRUISE M offers a tailored MPET heat exchanger component that allows for detailed parameterization of geometry, pressure drop and heat transfer. To support this often demanding work, a new dedicated parameterization wizard is released with this version of CRUISE M.
You only need basic geometric information about your MPET and reference data from measurements or other sources that characterize its behavior under different operating conditions. After a parameterization process, which takes only a few minutes, all parameters are automatically transferred to the genuine MPET Heat Exchanger component, which is then ready to be used in any kind of a VLE circuit.
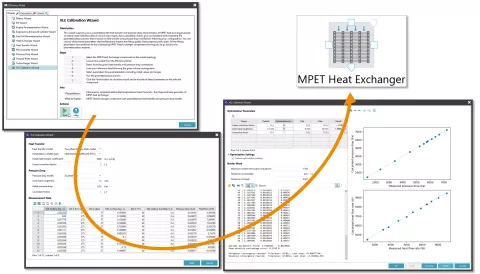
Pre-dimensioning of heat exchangers according to requirements and operating points is an essential task for simulation engineers and indirectly for the tools they use. The heat exchanger dimensioning shall be derived for given geometrical designs and flow patterns at specified powers and mass flows. This version of CRUISE M supports this task with a tailored wizard, helping you to create a completely parameterized gas-liquid heat exchanger from purely geometrical data in the absence of measurements. The application of dimensionless correlations allows for changing component sizes while preserving the fundamental correlations derived by the wizard.
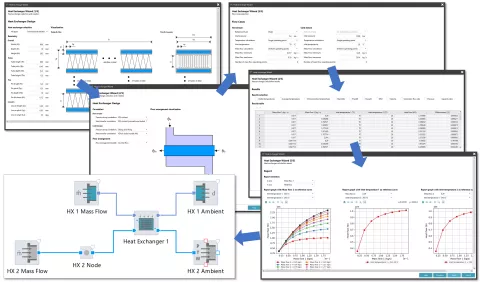
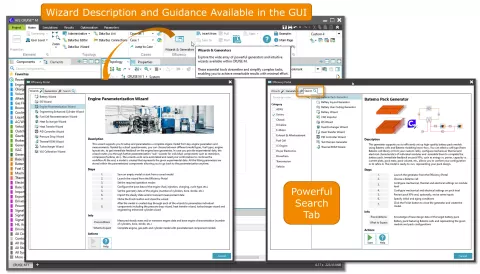
Efficiency is crucial when setting up comprehensive models and parametrizing individual components based on experimental reference data. CRUISE M has been supporting these key areas for many years with a family of more than 20 different generators and wizards. Generators help you set up comprehensive model layouts in the shortest possible time, while wizards provide dedicated parametrization workflows based on experimental or other reference data.
All the powerful functionalities provided by wizards and generators are bundled in a new self-explanatory front end, CRUISE M's Efficiency Portal. You can launch it directly from the ribbon, search for different wizards and generators and learn about the scope, application steps, preconditions and expected results of the different tools.
When sharing model FMUs, it is advisable to test them upfront. Equipping an FMU with input signals and monitoring all outputs is straightforward in CRUISE M. However, when the number of input and output channels increases, this task might turn cumbersome. CRUISE M helps to accelerate it with a new Test Harness Generator.
You can launch the generator from the Efficiency Portal for any model that is meant to be FMU exported. With that, you are guided to a configuration page where you can assign a certain input type from a drop-down menu for each input channel. The new created model holds nothing but three connected elements: the FMU, the inputs and a monitor for the outputs. Ready to run.
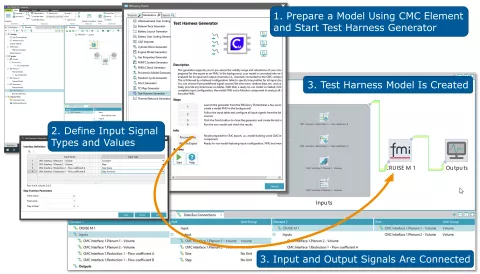
Simulating electrical networks on its own is a computationally demanding task and extending it with FMUs can turn it into a true challenge that calls for any possible specialization to be fast and robust. CRUISE M offers such an approach with its new electrical FMU component. You can load either a co-simulation or model exchange FMU of an electrical component and you can configure its kind. Four options are offered, current- or voltage-driven inputs with and without additional information on the current or voltage sensitivity. With that, you are all set to start a simulation, and CRUISE M efficiently invokes your component model into its equation system.
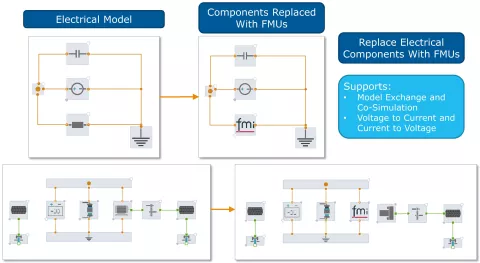