Latest News
See what drives us and explore our latest developments.
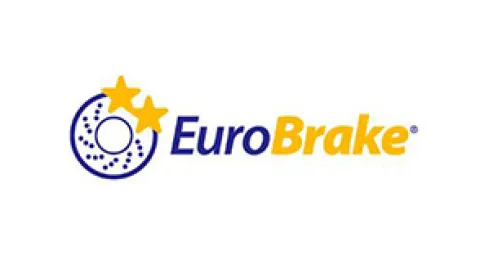
- News
AVL reaffirmed its leadership in sustainable mobility innovation by participating as a Gold+ sponsor at EuroBrake 2025, the world’s leading conference on braking and friction systems.
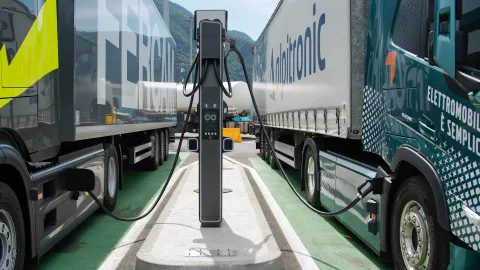
- News
AVL Italia contributes to the A22 project with Italy’s first megawatt charging station for electric trucks, installed at Bolzano South in the Firmian parking area. The station will integrate energy storage to
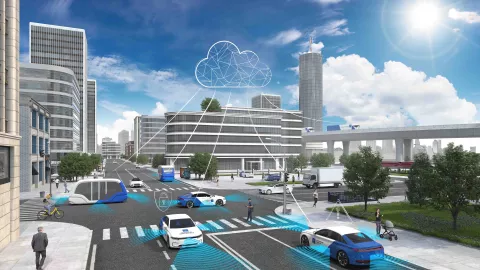
- News
Join us at the ADAS & Autonomous Vehicle Technology Expo in Stuttgart on May 20 - 22, 2025. Discover groundbreaking technologies driving autonomous and ADAS applications and approach our experts at booth #9222
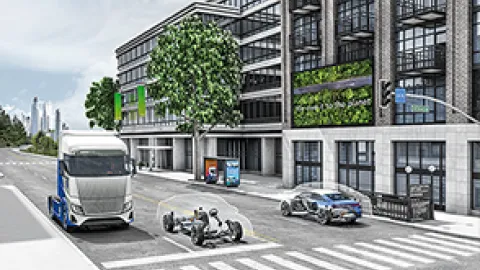
- Expert Article
Navigating the Shift from Combustion to E-Mobility – Insights from Matthias Fail

- News
Future Technologies and Sustainability combined at AVL Tech Center Steyr
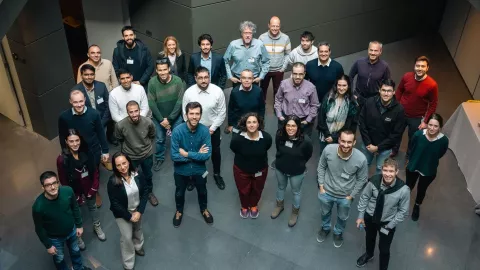
- News
The European MARBEL project consortium met at Applus+ IDIADA in Santa Oliva to review progress and plan next steps for developing advanced batteries for electric vehicles. The meeting included workshops, lab
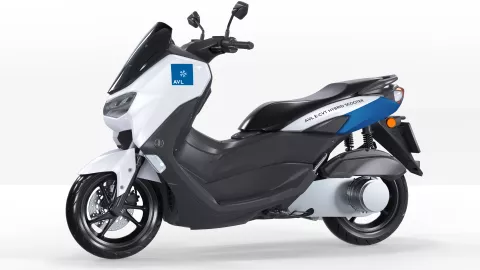
- Expert Article
Upcoming, increasingly stringent greenhouse gas as well as emission limits demand for powertrain electrification across all vehicle applications. For two-wheelers, motorcycles and all-terrain-vehicles (ATV) the
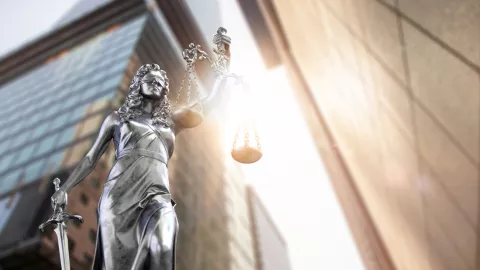
- Expert Article
Invisible to the naked eye, yet increasingly on the radar of policymakers, ultrafine particles (UFPs) are quietly shaping the future of air quality regulations. What does current legislation in Europe look like
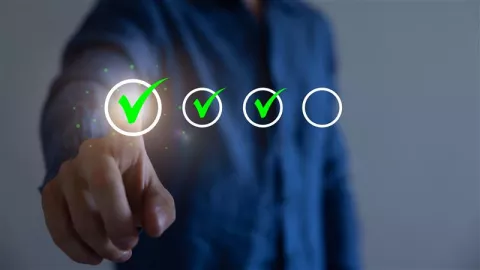
- Expert Article
Discover how advanced measurement techniques are transforming air quality monitoring and why focusing on ultrafine particles is essential for protecting public health and the environment.
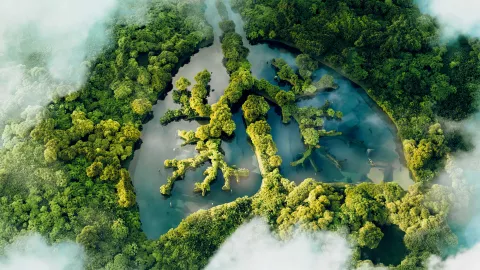
- Expert Article
Discover how these tiny pollutants penetrate our bodies, impacting respiratory and cardiovascular health, and learn about the cutting-edge technologies that can help us monitor and mitigate their effects.
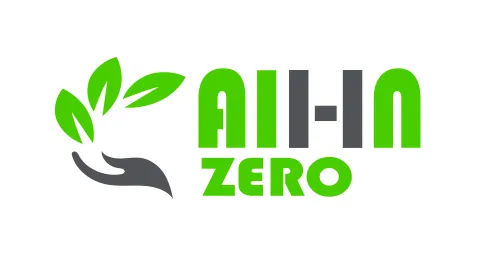
- News
On September 23-24, 2024, the ALL-IN Zero project team convened at AVL Ibérica’s facilities in Mataró, Barcelona. This meeting marked a significant milestone as the project reached the halfway point of its four
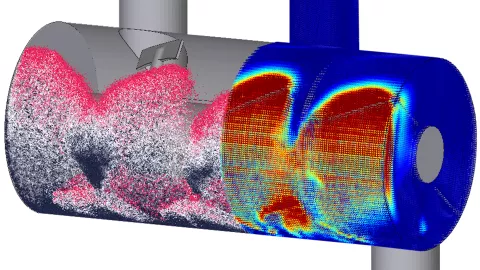
- News
AVL and InSilicoTrials (IST) have entered into a strategic partnership to integrate AVL FIRE™ M into the InSilicoTrials AI and modeling and simulation platform.