In a project or during a development cycle, the cost of design errors increases exponentially as the project progresses. The earlier one can test subsystems in the context of the entire vehicle, the easier it is to identify errors early on and avoid cost escalation.
One challenge engineers face is that the individual components of a vehicle are often not only developed in different teams using their own model. It is not uncommon for the teams to also use other tools or for individual components to be supplied externally. This is exactly where Model.CONNECT comes in. With its easy-to-use interfaces to leading simulation tools as well as open interfaces for customer-specific integration. If the co-simulation models are distributed across different companies, the software enables collaboration without having to exchange the models. Your sensitive data is thus protected.
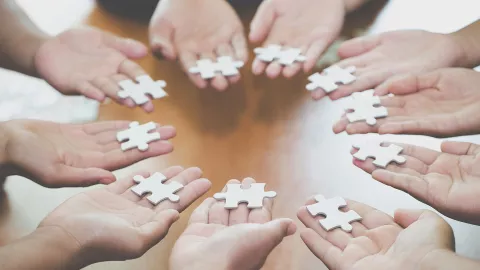
Verification
Confirm design decisions early and across teams using virtual prototypes.
Reduce Costs
Avoid cost escalation through virtualization and frontloading of integration tests.
Sustainability
Reduce the number of physical prototypes through mixed reality approaches.
Collaboration
Enable cross-functional collaboration.
Model.CONNECT is designed to couple different simulation tools and models. The software analyzes models and displays the input and output signals (I/O signals) in the user interface. In the next step, you can connect the signals yourself or the connections can be defined automatically in the connection wizard or through the programming interfaces (API).
Once the co-simulation setup is prepared, the simulation can be executed.
Model.CONNECT includes multiple coupling mechanisms and co-simulation engines to ensure optimal integration flexibility and simulation performance. Patented signal stabilization algorithms enable even better simulation performance and quality of results. The job management system supports sequential and parallel execution on a local machine or in cloud computing clusters.
Global parameter variations for optimizing any model parameter in the overall system context can be performed and evaluated with just a few clicks.
Thanks to the extensive scripting support, all tasks can be automated and integrated into fully automated test pipelines (CI/CD).
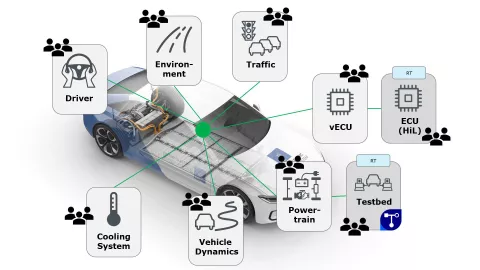
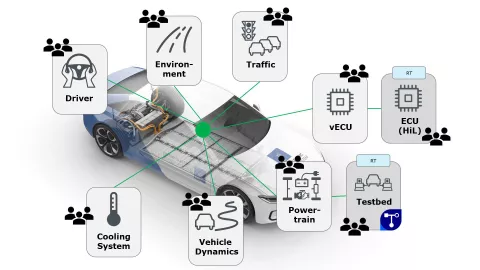
Flexible Interfaces
More than 30 interfaces to industry-leading simulation tools – including custom user interface support and real-time interfaces.
High Performance
First-class co-simulation engine with maximum performance and patented signal stabilization algorithms.
Fully Automated
Comprehensive scripting support for modeling test automation and toolchain integration as well as analysis of simulation results.
Collaboration
Promotes the sharing of results and insights between different departments to add value.
Coupling
Reliable synchronization of signal values from any number of tools even at different solver frequencies.
Standards
We are actively involved in standardization committees such as Modelica and ASAM and implement the latest versions of these standards (FMI, SSP, XCP, ...) in Model.CONNECT.
User-Friendly Setup of the Co-simulation Topology
Interfaces are simply dragged and dropped into the active system. After the respective model or project file is selected, the software captures the input and output ports. In the next step, you can choose to connect these to the ports of other models either manually or automatically. In the process, Model.CONNECT recognizes and checks the data types and physical units and converts different units, such as velocity output in m/s to velocity input in km/h.
Global Parameter Management
Model.CONNECT brings together the parameters of the individual models in a global parameter management. You can create test cases with concrete parameter values either manually or automatically with the included optimization tools. Parameter scripts in Python syntax allow you to calculate parameter values based on other parameter values.
Optimization and Job Management System
An integrated job management system allows you to define test cases with concrete parameter values. You not only have the choice between sequential or parallel execution. You can also choose whether the simulation should take place on a local computer or in a cloud computing cluster. Complex parameter variations are supported by over 15 active optimization algorithms and interfaces to external optimization tools.
Interactive Performance Analysis
The values of all signals can be followed live in different visualization modes. The performance analysis mode helps you to identify bottlenecks or real-time violations of the individual models. This allows you to systematically optimize the performance of the overall system and ultimately save time and costs.
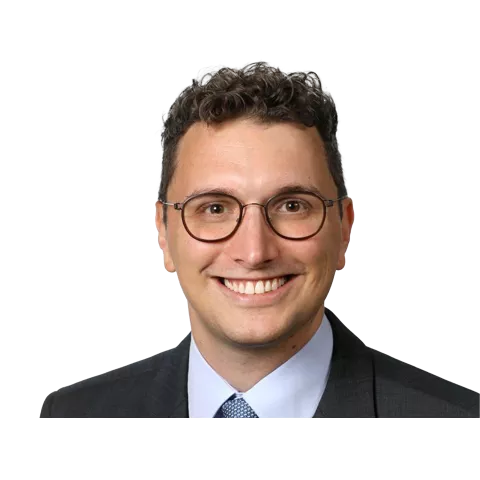
With the help of Model.CONNECT™, we can design our entire platform of simulation models in a modular way for co-simulations and thus gain significant flexibility. For our research, we can therefore build on our existing know-how and develop complete models even more efficiently.
– Maximilian Stumpp, Research Associate, Institute for Combustion Engines and Vehicle Drives (VKM), TU Darmstadt
Model.CONNECT™ Product Sheet
DownloadAVL White Paper - How to Maximize the Efficiency of ADAS/AD Development and Validation Using Simulation
The introduction of advanced driver assistance systems has become an important innovation driver. Safety constraints, emission legislations, driver comfort and short development times are the most important challenges for car manufacturers and suppliers alike. Discover in our white paper how to maximize development efficiency, saving time and money, by our open and integrated model based development approach.