Developers and manufacturers of e-drives (e-motor + inverter) require highly versatile testing capabilities to ensure coverage of various types of units under test (UUT). They need the possibility to validate their e-motors and even control strategies and algorithms without having the inverter hardware available. Cost pressures are also increasing, and development efficiency in terms of time and cost remains a crucial factor.
If you want to learn how our customers use the Universal Inverter, download our use case collection.
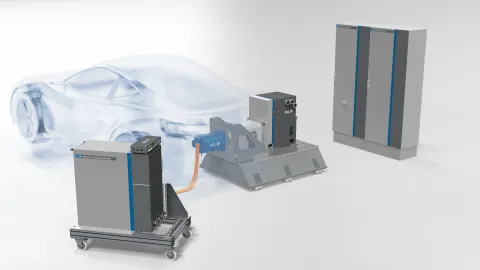
E-Motor Portfolio
Testing a wide range of e-motor types is becoming an industry standard.
Vehicle-like Testing
Creating a test setup that comes closest to real vehicle conditions.
New Technologies
Test an e-motor, even if the inverter is not yet available (for example a SiC MOSFET inverter up to 1000 VDC).
Test Proprietary Control Software
Test how your software behaves at an early stage.
The flexible SPECTRA Universal Inverter can be used to test various motor types and offers unique performance. It can be integrated easily within every automation tool and the user is guided through the inverter configuration process. A minimum amount of motor data is needed to be able to start with testing. The fast 1 MHz control via FPGA (field-programmable gate array) technology complements the solution and provides superior control.
- Supported motor types: EESM, PMSM, IM
- Automation tool interfaces: EtherCAT, Modbus, CAN, XCP)
- Supported Encoders: Resolver, SinCos (SSI)
- 2 and 3 Level Operation
- Automatic Resolver calibration procedure
- Cogging torque & ripple compensation functionality
- Extremely versatile and open control logic
|
One Device for Every Motor
The Universal Inverter supports not only the standard motor types PMSM and IM, but also EESM.
Easy to Use
A guided workflow via software and automatic test procedures guarantee easy setup of motor types and sensors.
Flexible and Cost Saving
The universal inverter can be placed close to the motor to avoid losses due to long cables.
High Performance
Up to 1,260 Arms continuous current without de-rating over switching frequency as just one highlight of performance.
Inverter Emulation
The possibility to validate the control structure at an early stage speeds up inverter application development and reduces the number of prototypes.
Wide Range of Modulation Schemes
Access to a wide range of modulation schemes allows testing conditions close to the real traction inverter.
AVL SIGNATURE Line – Brochure
Superior Technology – with AVL SPECTRA™ Inside.
AVL SPECTRA™ Universal Inverter – Solution Sheet
Versatile testing device for future-proof e-motor and inverter development.
Presentation – Applications Universal Inverter
Compiled key use cases of the Universal Inverter.
AVL E-Mobility Testing Solutions – Brochure
From battery to full vehicle, from products, to test systems to whole test facilites – learn how we can support your testing needs.