With extensive experience in NVH powertrain testbeds, we provide high-quality acoustic test environments for e-axles. Our simulation-optimized design minimizes sound reflections and guarantees exceptional NVH performance. Every component, including acoustic enclosures, is engineered for optimal efficiency and ease of use.
The testbed is equipped with movable loading units that allow flexible adaptation to different test specimen sizes. Hinged acoustic enclosures provide easy access to maintenance areas, ensuring efficient and straightforward upkeep
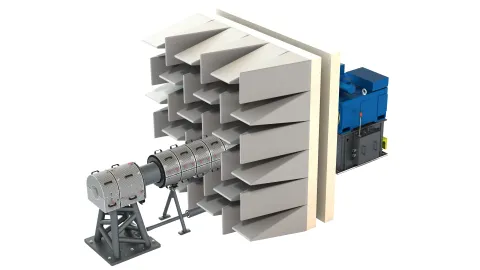
We provide innovative NVH testing solutions that enable precise simulation of high-speed vehicle operation. With a maximum rotational speed of 3,000 rpm, our test systems allow for accurate performance assessments under real-world conditions.
Our advanced driveline design, including intermediate bearings and wall pass shafts, ensures the reliable transmission of a constant torque of up to 10,000 Nm. The test setup is highly flexible, offering a continuously adjustable track width of up to 600 mm per side, totaling 1,200 mm. Additionally, the wheelbase can be adapted over a wide range to accommodate various testing requirements.¹
To maintain an optimized acoustic testing environment, AVL guarantees a maximum noise level of just 55 dB(A) even at peak operating speeds. This ensures precise NVH analysis without interference.
¹ Only for 4WD configurations.
|
Optimized Space Requirements
Extremely low-noise performance as well as optimized shape and surface of the test equipment, for a minimum space requirement in the NVH chamber.
Adaptability to Various Propulsion Systems
Flexible and variable design for fast adaptation to different propulsion systems without compromising NVH performance.
High Performance
High torque capability with precise torque control.
Efficient Assembly and Replacement
Easy, fast assembly and replacement of UUTs for minimal downtime and high test efficiency.
Low Noise Intermediate Bearings
The load system’s intermediate bearings are specifically designed for NVH applications to ensure smooth operation with low noise and vibration levels. This ensures the best possible focus on the test object.
Infinitely Variable Adaption Systems
Both track width and wheelbase can be adjusted in infinitely variable increments. This ensures perfectly repeatable mounting conditions for the UUT.
Quick Setup Time for Reduce Down Time
In addition to the focus on NVH performance, great emphasis is placed on ease of use of the test system. This reduces testbeds downtime and optimizes productivity.
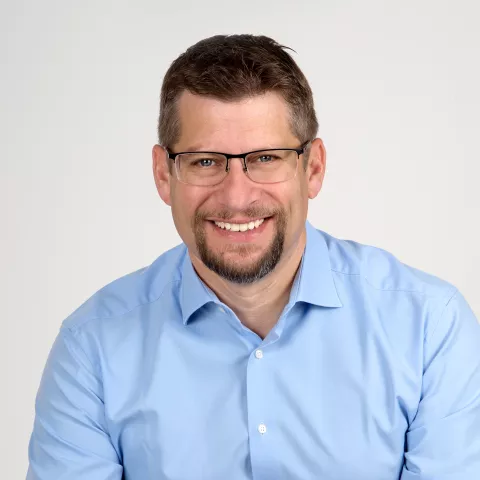
NVH is not only about improving noise on vehicles and powertrains, much more it’s about setting up a brand sound, inspiring the passengers of modern cars during their ride. With our NVH test systems and solutions we provide a high class development platform for sound development and drive the pleasure of tomorrow’s mobility.”
– Joachim Schmidt, Department Manager, AVL List GmbH
AVL E-Mobility Testing Solutions – Brochure
From battery to full vehicle, from products, to test systems to whole test facilites – learn how we can support your testing needs.
AVL E-Axle Testing Solutions – Brochure
Validating Integrated E-Drive Units with Advanced E-Axle Test Systems.
AVL NVH Test Systems – Brochure
Our commitment to silence.
AVL E-Axle TS™ NVH – Solution Sheet
Our commitment to silence.
Case Study – “NVH Testing for Vitesco”
Unique NVH test environment offers wide variability in testing capabilities.