E-Mobility Engineering
Electric vehicles are a key enabler of sustainable mobility. We adopt new approaches to shape and simplify the transformation for you. When it comes to developing battery electric and fuel cell electric vehicles, we offer the following:
- All engineering services – from the individual component to the system and integration into the vehicle
- Support with the development of a coordinated overall solution
- Energy efficient technology platforms
- A global network of facilities
Our observations go beyond the vehicle – we also consider the necessary charging infrastructure and primary energy production. At the same time, we make sure to optimize the overall systems– to make electric vehicles affordable. We work with you to find the optimum when it comes to costs and sustainability throughout the lifecycle.
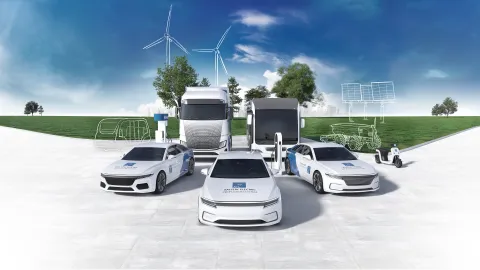
Automated and Connected Mobility Engineering
Advanced Driver Assistance Systems have become an integral part of modern vehicles. Integrating these functions to the full range of vehicle variants with local requirements is complex. And new, innovative approaches for the higher level of automation also need to be made ready for series production.
Advanced Driver Assistance Systems (ADAS) and Autonomous Driving (AD) require constant development and validation of new functions that meet current standards and legislation as well as end customer expectation. They are integrated into vehicles both as safety and comfort functions. We support you in this task with the utmost efficiency, from defining targets to developing the white-box software and validating the functions, including cybersecurity – both virtually, on our proving grounds and also on real roads.
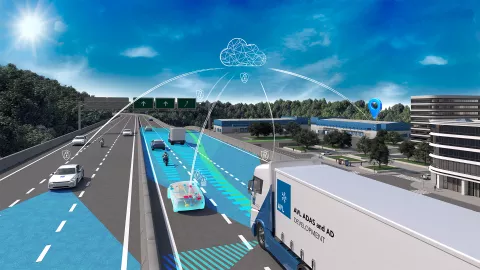
Vehicle Engineering
Our focus is on virtual and functional vehicle development, as well as on integrating systems into the vehicle. This allows us to consider and optimize functions and control systems holistically in the context of vehicle architecture at an early stage. Which is how we boost the maturity of the concept while also reducing the development time and effort required.
Overall, we guide you towards new mobility. Whether passenger car or commercial vehicles – we reconcile your individual requirements with the expectations of end customers. As your partner in vehicle engineering, we create aligned overall vehicle concepts for you while balancing vehicle attributes and the relevant vehicle system.
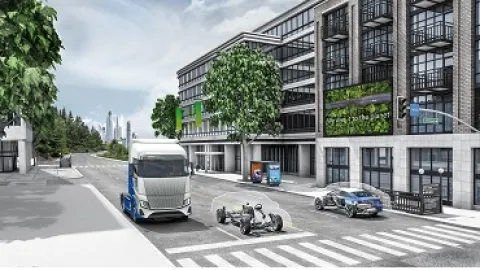
Hybrid Propulsion Engineering
The aim of hybrid propulsion is to combine an internal combustion engine and an electric engine efficiently, to make best possible use of the advantages of both types of propulsion systems. We develop and optimize your hybrid propulsion system: thanks to our extensive knowledge of the internal combustion engine, e-motor, hybrid drive, and power electronics we can balance low consumption and compliant emissions with optimal driveability.
Specific software and functions, including calibration, deliver the optimum operating strategy. Systems engineering and model-based simulation enable us to reduce your prototype and testing efforts in SOP vehicle derivative projects by up to 30 %.
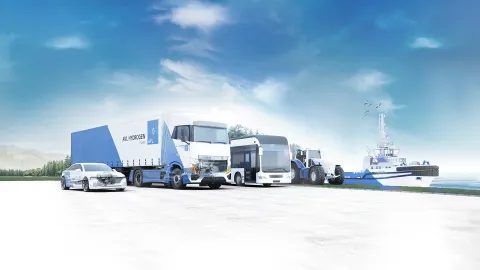
Level up your Mobility Engineering
With innovative methods and technologies ready for series production, AVL has been driving the development of all types of mobility systems for many years now. Talk to our experts today!
Explore our broad portfolio of engineering services across all industries with a focus on e-mobility, automated and connected mobility, vehicle, hybrid propulsion and energy system engineering.
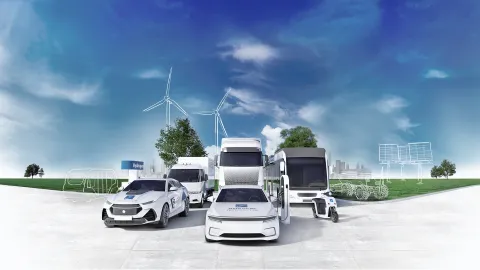
We offer rapid, competent support around the world. Our subsidiaries, global network of experts, and our extensive expertise give us a global presence – as your reliable partner for ambitious mobility engineering. We have all the relevant topics covered – from e-mobility to ADAS/AD and overall vehicle development.
5,700+
mobility experts worldwide
370+
engineers in the areas of ADAS and AD
480+
engineers for passenger car concept design
450+
fuel cell engineerings globally
120+
engineers for thermal systems and HVAC
900+
battery projects executed
5
Fuel cell tech centers globally
15
ADAS/AD centers of excellence globally
Moving steadily into the future: Find out what’s brand new in the field of mobility engineering.