Transformation poses new requirements on testing solutions
The need for CO₂ reduction, tougher legislative requirements and highly varying consumer demands create unprecedented challenges to vehicle manufacturers and their partners along the value chain. With many different types of propulsion systems, it is becoming even more difficult to meet the development targets of speed, quality, and costs. AVL with its experience in the automotive industry of more than 70 years helps you to find the ideal combination of tools, processes and methodologies that best supports your development work with maximum efficiency to quickly bring new models to the market.
The right testing infrastructure to master your challenges
We offer you the most advanced and accurate testing solutions for every step of the propulsion development process – from the first concept study all the way through to series production. Our great variety of application solutions connect different development environments and incorporate the latest methodology approaches. Depending on your application, our tools support the frontloading of development tasks, helping you to save time, increase quality and keep costs under control. We lay the foundation for efficient development operations in the new age of the connected vehicle.
From testing solutions for E-Mobility, Fuel Cell, Automated and Connected Mobility, and ICE / Hybrid propulsion systems to standalone measurement equipment and software to customer service solutions, we have the expertise to support the optimization of your testing and validation programs.
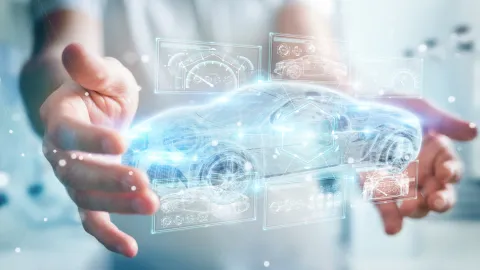
E-Mobility Testing
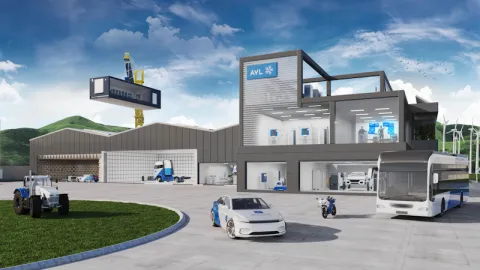
With the electrification of the powertrain developers face many new challenges. Electrification does not only increase the range of solutions, but also the number and type of design options. Therefore, a partner with both specific application know-how and a holistic perspective on the system is critical. We provide you with exactly this required expertise.
Hydrogen Testing Solutions
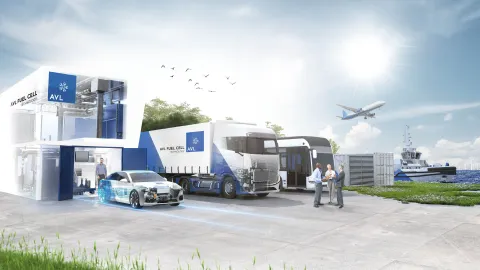
The widespread introduction of hydrogen is a necessary and essential part of the path to a climate-neutral future. AVL is ideally equipped to support and help shape this transfer. In terms of content, we provide extraordinary expertise in the fields of engineering, simulation and testing and act as a reliable innovation and development partner. With our test solutions, we support you specifically with your challenges, from development, through industrialization, to further operation. Depending on the technological maturity of your product, the test solutions offer you full flexibility within the planned development tasks or a customized proportion of supporting and automated functions, if quality assurance in the production environment is involved. The guarantee of safe operation is obligatory and is of course also mapped.
Automated and Connected Mobility Testing
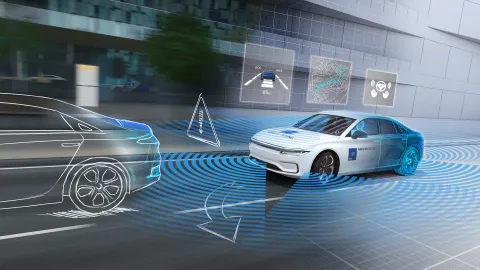
The future of mobility will be highly automated. Most new vehicles already feature some sort of assistance systems and rapidly advance into more complex functionalities. But with such technological progress comes increased development effort, complexity, and time-to-market pressures. We offer a great variety of solutions for the calibration, verification, and validation of Advanced Driver Assistance System (ADAS) and Autonomous Driving (AD) features to ensure robustness, reliability, performance quality, safety, and user acceptance.
ICE/Hybrid Propulsion Testing
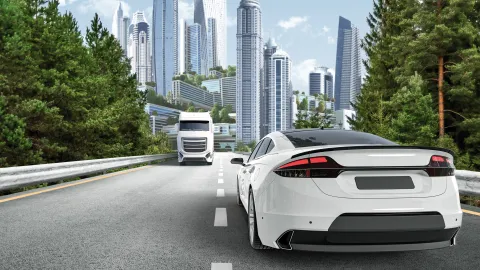
Vehicle manufacturers and suppliers are facing global challenges and need to develop solutions to avoid further greenhouse gas emissions and improve local air quality. To meet these challenges, the industry must continue to optimize the performance of traditional combustion engines and invest in the hybridization of powertrains. We are highly committed to helping you develop zero-impact emission mobility solutions with a tailored offering that perfectly fits to your specific needs. Our holistic approach enables us to support you in the management of even the most complex testing tasks.
All Testing Products and Software
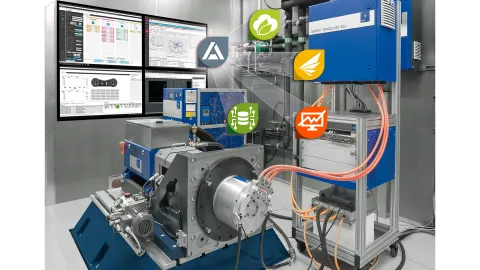
We provide you a comprehensive range of standalone testing products and software for every need. Our broad portfolio of testing devices comprises advanced measurement technologies, battery test and emulation products, electric dynamometers and drives, as well as emission analysis and measurement solutions. In addition, we can offer you a great variety of software from test system automation to connected development tools.
Customer Services for Testing Solutions
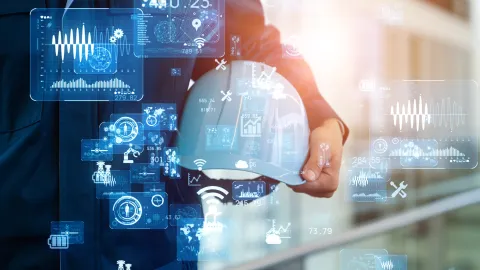
At AVL, we understand the importance of the availability and usability of test equipment throughout the entire product life cycle. We aim at reducing total cost of ownership, increasing technical availability, and securing measurement data quality of test equipment. In this way, AVL Customer Services help to avoid unplanned testing cost, reduce test repetitions, and achieve meaningful testing results.
Tech Center Solutions
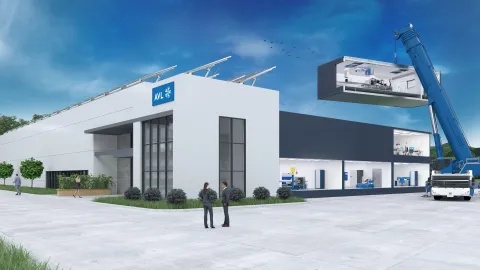
We offer complete turnkey solutions for testing facilities: from requirement analysis and design to build up and operation of it. Our expertise lies in the integration of test systems into a building and establishing all utility interfaces. Our future-proof solutions are based on AVL’s holistic understanding of development and testing. We support customers in all project phases from consultancy, design engineering and procurement to the execution of the project.
AVL’s comprehensive worldwide network of experts allows best customer vicinity, ensuring consistent and connecting testing fields globally. Wherever your R&D challenges take you, we are always close at hand, ready to provide the service you need.

> 70
years of experience
> 5000
employees worldwide for testing solutions
> 30
countries covered by the global network
> 7000
testbeds installed worldwide
> 80
turnkey projects
Here you can find information about product news, fairs and events, and other updates.