OEMs, battery, and cell suppliers have to continuously develop new packs and cells for the evolving automotive market. For battery electric vehicles (BEVs), the mileage range is a key factor, making the capacity of battery cells and packs crucial. Besides capacity, current and voltage are central to battery development. As a result, the test systems for validating battery cells and packs need to be state-of-the-art.
From individual test products to integrated system solutions and complete battery test facilities, you have come to the right place for battery test expertise. Our software and hardware portfolio is complemented by holistic support options and application service.
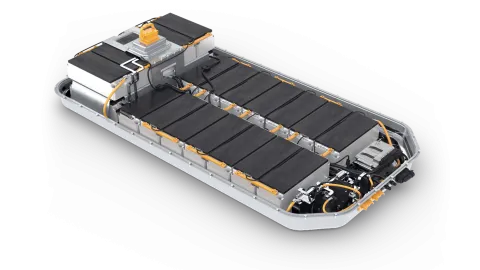
Testing Battery Cells
A battery cell test system is a testbed that includes at least one temperature chamber suitable for testing lithium-ion batteries, a cell cycler in the appropriate current and voltage range, and an automation system. The size of the cell determines which of the various chambers with special safety equipment is required. In addition to the chamber, the cell cycler and the required current and voltage ranges must be aligned with the respective cell.
Along with our test system, we also offer automation software for performing all types of fully automated tests. The products mentioned above, but also special equipment such as Electrochemical Impedance Spectroscopy (EIS) can be integrated and operated within our AVL Battery Cell TS™. We also offer software solutions for running entire laboratories with several thousand cell test channels via AVL Lab Management™ for Battery.
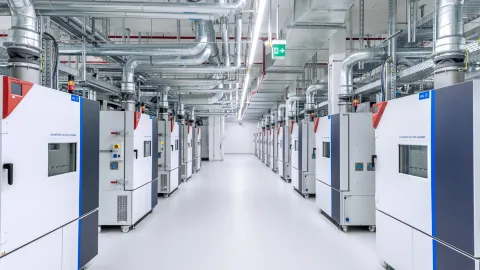
Testing Battery Modules and Packs
OEMs and battery suppliers have to continuously develop new packs for the evolving mobility market. For battery electric vehicles (BEVs), the mileage range is a key factor, making the capacity of battery cells and packs crucial. In addition to capacity, current and voltage are central to battery development. As a result, the test systems for validating battery packs need to be state-of-the-art.
We offer advanced solutions for battery pack and module testing, including containerized and modular test systems. Our technology measures all critical parameters under various environmental conditions and features multifunctional interfaces for seamless integration with additional testing tools. By combining customer-focused development services with independent test equipment innovation, AVL provides a holistic approach to addressing the challenges of battery testing.
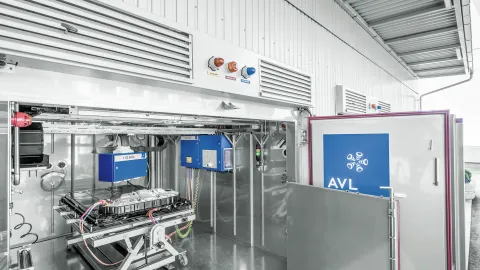
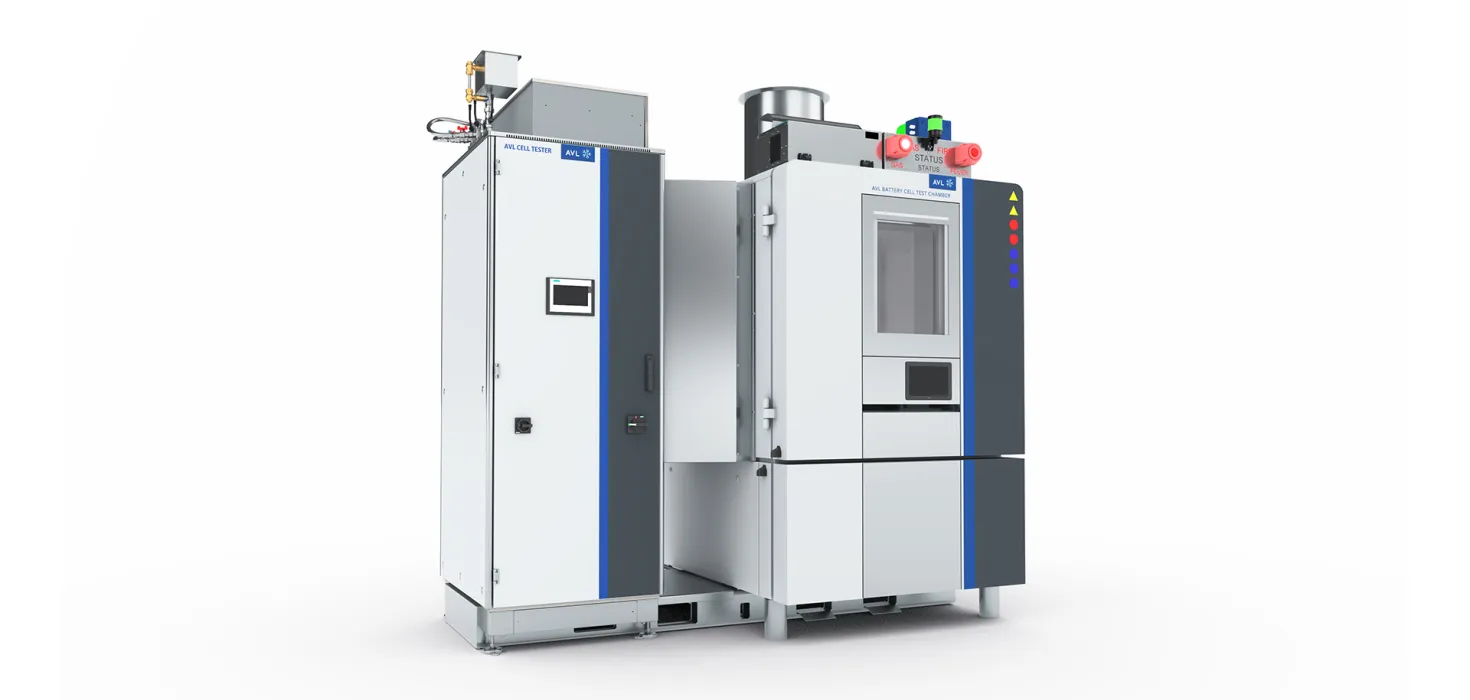
AVL has developed battery cell cyclers (AVL CELL TESTER™) to improve and accelerate electric vehicle development. These bi-directional, multi-channel DC power supplies test, diagnose, characterize, and validate battery cells, achieving output currents from ±2 A to ±2,400 A. The Cell Tester uses a unique current measurement technique for best-in-class accuracy (0.01% of actual value) among high current cell cyclers. This reduces test programming complexity, ensures consistent accuracy, and provides reliable results. It also reduces test time through accurate coulombic efficiency analysis. → Learn more
Testing the Integration of High-Voltage Components
High-voltage systems are complex and dangerous if not properly designed and tested. The AVL HV System TS™ E-Integration provides a safe environment to test HV systems, which helps to prevent accidents and injuries. Besides that, cost-effectiveness is very important. Testing HV systems in a real-world environment can be expensive, time-consuming, and risky. The AVL HV System testbed provides a cost-effective way, without the need of a chassis dyno, to test HV systems before they are implemented in vehicles, which can help to reduce development time and costs.
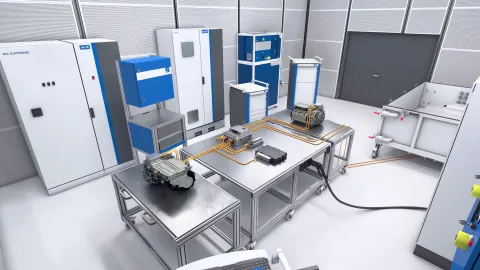
Testing the Charging and Discharging of Electric Vehicles
New charging standards and norms regarding connections, communication, safety, etc. had to be established between OEMs and the industry in recent years. It is desirable to move charging test activities to a controlled test environment to reduce test costs, accelerate development, improve V&V, and enhance quality and customer experience. Simulated charging enables testing of various communication protocols as well as misuse or failures/ malfunctions of charging stations. For AC charging, different mains supplies can be tested depending on the region, e.g. JP, US and EU.
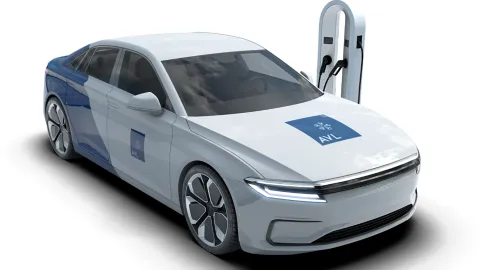
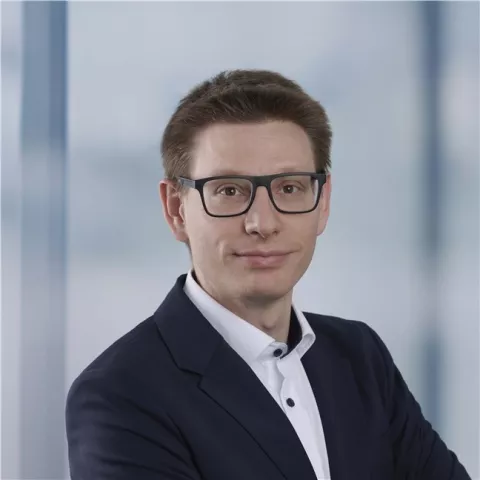
When it comes to batteries, there are countless opportunities to find the right development partners and manufacturers. Here, nuances decide to prevail in the market. As a globally positioned company with knowledge from battery development, simulation and production, AVL is the reliable and competent partner in the field of test systems for batteries.”
– Reinhold Hetzel, Global Business Unit Manager, AVL List GmbH
At AVL, we have an unwavering commitment to quality, reliability and innovation in battery safety testing. With deep industry expertise, we develop comprehensive safety solutions tailored to the unique needs of our diverse customer base, enabling them to meet the highest safety standards. The AVL Safety Chamber ensures advanced testing for maximum safety.
At the heart of our battery safety strategy is the AVL Safety Chamber, a state-of-the-art, modular test system designed to perform rigorous environmental and abuse tests on battery cells. It ensures that batteries can withstand the harshest conditions they may face in real-world applications. Partner with us to future-proof your battery technologies with industry-leading safety test solutions. Get in contact with us right now.
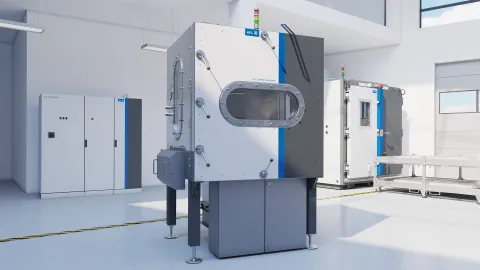
AVL Battery Testing Solutions – Brochure
Learn more about our holistic battery testing portfolio and solutions.
AVL Battery Testing Solutions – Whitepaper
Learn more about our testing approach and solutions offerings.
AVL Cell Testing Solutions – Brochure
To master the heartbeat of the battery. From single channel to automized lab testing.
Success Story – “Battery Testing for Lilium eVTOL”
Expertise and test equipment for success in battery development.
Success Story – “Battery Testing for LABCO”
How AVL supported LABCO BTC in entering the world of battery development.
Success Story – “Valmet Automotive”
AVL E-Mobility Testing Solutions – Brochure
From battery to full vehicle, from products, to test systems to whole test facilites – learn how we can support your testing needs.
AVL Battery TS™ End Of Line – Solution Sheet
Tech Center Module – AVL Battery Pack TS™ – Solution Sheet
The fast track to battery testing excellence.
Battery Testing: Aviation – Solution Sheet
Boost your battery test process.
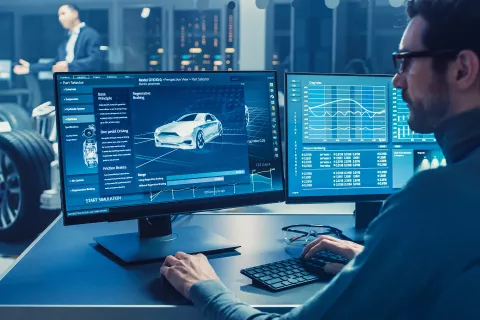
How can the time to market for new batteries and electric vehicles be shortened? AVL offers comprehensive software solutions to optimize your battery testing performance.
Our holistic approach combines lab efficiency through automation, test optimization via virtualization for faster and reliable results, and advanced data analytics using AI to extract valuable insights from various sources.
This will help you get your products to market faster while ensuring high quality performance. Learn more about AVL’s approach and explore our software solutions to optimize your battery testing process now.
Thanks to AVL affiliates all over the world we are close to our customers with a global footprint. With our experience from different customer types, like battery, vehicle or energy storage manufacturers, we are able to continuously improve our test systems. New entrants as well as well experienced OEMs and Tier 1 and Tier 2 suppliers and test institutes rely on the support of the global AVL network. Our affiliates represent AVL directly on customer site.
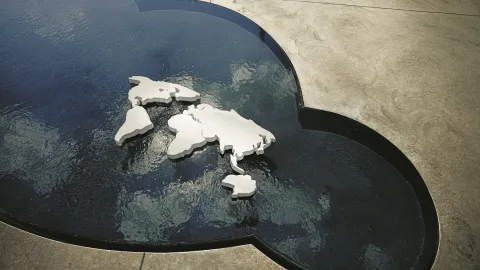
> 200
project managers in Graz, and globally
> 50
battery testing projects per year worldwide